Many of the project goals focused on the creation of a cohesive and livable, mixed-income neighborhood. In striving to reach this goal, SHA and the design team generated many new ideas, which have helped to gain national recognition for the project. In addition to the community development focus, High Point has also made special effort to incorporate sustainable construction strategies. The project recycled and reused many materials from demolition, including wood from felled trees, found boulders and the concrete from old building foundations. They also saved and protected almost 80 of the most beautiful and valuable trees onsite. While these are nice touches, High Point’s most notable step toward sustainability is the Natural Drainage System (NDS), used to manage storm water.
High Point encompasses 10% of the Longfellow Creek watershed – which has recently become Seattle’s most productive urban stream for salmon habitat due to many community efforts to reduce barriers and increase habitat quality. Despite its narrow streets and many parks, High Point’s redevelopment represents a significant increase in impermeable surfaces over the previous land-use patterns. As such, SHA and the design team worked with Seattle Public Utilities (SPU) to develop sustainable strategies for dealing with storm water. Based on another Seattle project known as SEA Street (Street Edge Alternative), SPU and SvR Design developed 22,000 feet of vegetated and grassy swales that store and treat storm water before discharging into Longfellow Creek. During smaller storms, rainwater will slowly infiltrate into the soils and eventually into the groundwater. During larger storms, water flow will be slowed before entering the creeks, thus reducing flooding and erosion of stream banks.
The NDS developed for High Point had never been built before – as was the case with many of the great ideas proposed by the project – which created many challenges for the contractors and designers. The challenges are most evident in the sequencing of activities. For example, Absher Construction won the General Contractor job, which for this large public project meant managing both the housing and the infrastructure. However, Absher, as an inexperienced infrastructure contractor, had some difficulty organizing the activities associated with the NDS and the permeable paving. In one case, an entire street bordering existing and inhabited homes was dug up early in the project before plans for the permeable paving were complete. This dramatically impacted the resident’s access to their property and caused significant inconvenience. Additionally, pouring permeable paving on an active construction site can be problematic because it needs to be protected from dust/dirt until the project is finished. The NDS and permeable paving also have very demanding functional and aesthetic requirements that are challenging to the contractor, such as limits on compaction, and techniques for watering and installing plants.
The contractors on this project have all won their jobs via a low-bid, thus motivating them to increase their profits by working fast and efficiently. However hasty construction increases the likelihood of mistakes. Contractors with their eyes on the bottom line are likely to either argue that mistakes ware not their fault or try to push them under the carpet in hopes that they are forgotten or overlooked. We saw many examples of this at High Point, such as windows on several houses that were improperly centered. The design team didn’t recognize this mistake until the houses were framed, painted and nearly ready to sell. In this case, the framing contractor who made the mistake will not have fix it because redoing the work would involve several other contractors who’ve already finished their bid.
A similar situation occurred early in the demolition process when Merlino, an infrastructure subcontractor, was charged with locating and removing all of the old building foundations scattered throughout the site. Later in the project grading crews discovered multiple buried foundations, revealing that Merlino did not perform the work they were paid to do.
A solution to the problems created by low-bid contracts is to use “time and materials” or reimbursable billing. In this way the contractor is only paid for the work that they actually do. In the case of Merlino, their failure to locate any of the foundations would mean they didn’t get to do that work – a sharp contrast from not having to do that work.
Another technique to increase profits for Absher during their bid solicitation was to incorporate extra time into each bid. They asked each sub-contractor to take their lowest bid and add two hours onto each task, giving room, if needed, to go back and make corrections, and allowing both parties to avoid the complications associated with a change orders. However, this strategy is now being questioned by the owner (SHA) who believes that the money from any unused bonus-time should be returned to them, rather than be realized as profit for Absher.
The High Point project had both successes and failures in controlling erosion. After demolition of the existing housing, the general contractor did a sub-standard job of placing proper erosion-control structures on the site. During heavy rains in the winter of 2003, significant erosion was washed into Longfellow Creek, prompting the hiring of an erosion control specialist (using reimbursable billing) to install new erosion control.
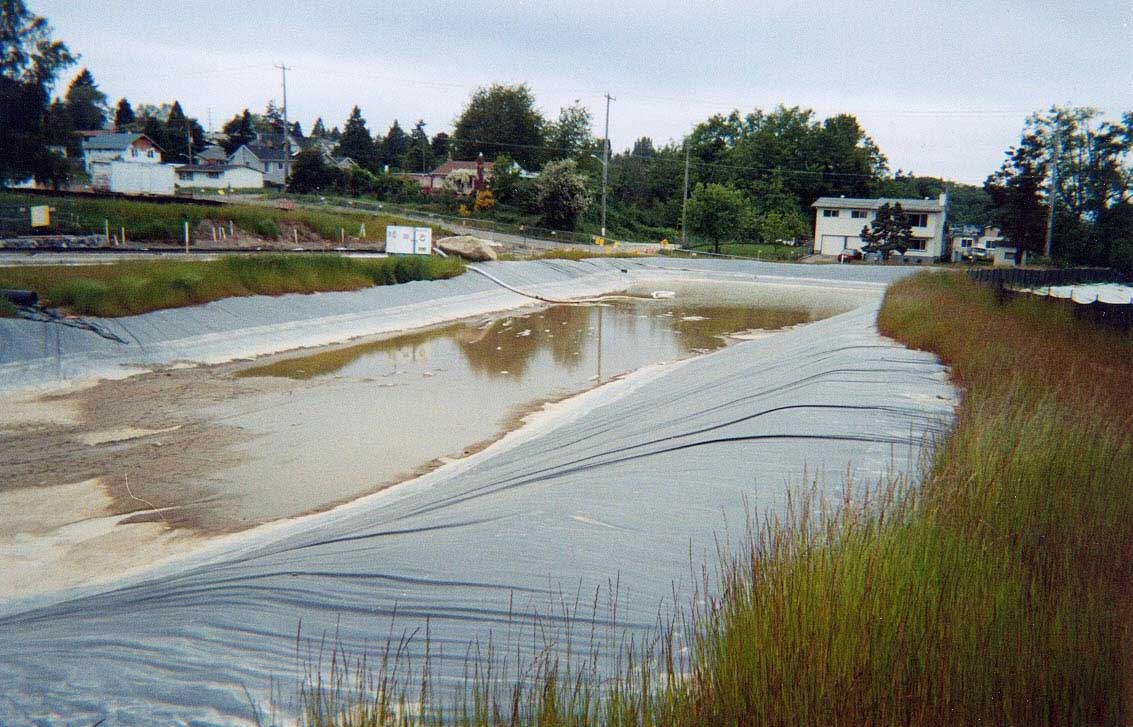
Currently, erosion control on site is handled with a variety of techniques. Several smaller sediment ponds around the site capture and settle runoff. These ponds feed into a larger pond from which the water is then pumped out. One problem has been that the suspended silt in the water is too fine to settle. A treatment called Chitoson, which binds with the silt and settles out, is being added to the water. Additionally, many areas of the construction site have been hydroseeded with wheat and clover to control erosion.
The existing soils at High Point were already highly disturbed from the site’s initial development. The High Point project had specific soil qualifications because of the performance needs of the NDS, particularly in the swales. Because using a proprietary mix for such a large site was cost prohibitive, SvR investigated a variety of ways to create the necessary soil mix. The initial strategy was to amend the existing soils, but their high silt content did not allow for proper soil drainage. SvR instead used Type 17 soils, the standard soil specification for utility back fill in Seattle, and amended them with 35% compost. Because of space limitations, this soil is being mixed off-site at Cedar Grove. Non-NDS soils are being amended in place by tilling in compost up to 8” deep (per spec). However, the soils are routinely tilled only 4-6” deep by the contractor, which is apparently not a big enough problem to make an issue of.
There has been some difficulty with balancing cut and fill on site. Although there was projected to be an equal amount of cut and fill, the challenge has been proper sequencing. The original intent was that the infrastructure construction would be two months ahead of housing construction, which would generate adequate proportions of cut and fill. However both projects were begun at the same time, thus creating shortages.
The contractor also did not properly protect the stockpile of fill during wet periods, resulting in stored soils being overly saturated. Wet fill cannot be properly compacted, thus is not usable. Although several techniques for drying out the soil were tested, a significant proportion has been rendered unusable and will be removed.
Great effort was made to save as many of the existing trees as possible. Although both DPD and SHA had an interest in saving trees, it was particularly valuable for SHA developers since mature trees make the properties look more established, and therefore increase the salability of the lots. SHA hired an arborist to inventory and evaluation every tree on the site. Critical root zone (CRZ) sizes were determined at a conservative estimate - one foot of CRZ per one inch of trunk radius. During the planning process efforts were made to save as many trees as possible, although this was sometimes difficult because the street alignment necessitated some removal. The CRZs also restricted the amount of allowable grading, which was a major challenge to site planners who needed to drain 50% of all the roof water onto the ground and into the swales. Phase I aimed saved about 100 of 350 trees, ultimately settling on roughly 75.
Incentives and disincentives were included in the construction contracts to make sure that no trees were damaged during construction. Each tree was clearly marked with fencing and labeled with its species name and estimated value. A $100,000 fund was set aside for later division among the contractors if trees were not damaged. Furthermore, a $1500 fine is leveled if contractors are caught disobeying the restrictions placed on the trees.
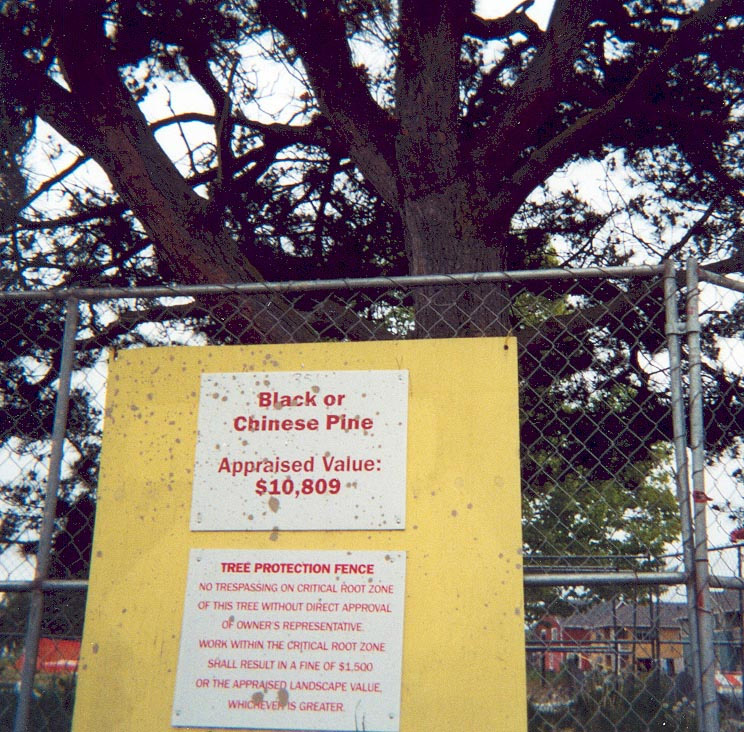
In addition, the wood from many trees was saved for use in future construction projects. Some of it will be used for park features like tables and a shelter house. Other wood is being used in the Pomegranate Center’s gathering places project.
There were a variety of other sustainable approaches taken in construction. The contractor was required to run bio-diesel in all of their equipment - something that was not done until the contractors were reminded of this commitment. Part of the way through the project, the contractors were also asked to turn off the engines of their equipment when idling, saving the contractor a whopping 50% in fuel costs. To control sediment and dust onsite and in the neighborhood, street cleaners run the site most days, and entrances are restricted, ensuring trucks utilize the paved wheel wash.
High Point is an ambitious project. Its implementation of new sustainable technologies on a large scale sets new standards, serves as a national model and provides many important learning opportunities. |