    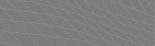  |
|
|
|
|
|
|
|
Cost/Benefit
Issues |
|
The manufacturing process
and application process have a number of positive and negative aspects.
Within the manufacturing process, the obvious positive feature is
the use of recycled materials. The waste products of lumber construction
can be reused in the plastic lumber mixture. The normal flaws of wood,
such as knots or bowing do no prevent the wood from being useless.
This greater capacity to use more of the tree cut for lumber is paired
with the use of post-consumer recycled plastics. |
|
|
|
The challenge of using
recycled materials is that of contamination. The chemical differences
and lingering substances on plastics make it hard to efficiently reuse
them. Fortunately, materials like plastic soda bottles are becoming
readily available. These bottles provide a constant, uniform source
of plastic without any hazardous residue. |
|
|
|
The application cost to purchase recycled
plastic lumber products averages 20% to 50% more than the price of
wood. Payback is typically two to four years when you factor in maintenance
and replacement costs. Many recycled plastic lumber manufacturers
guarantee their product to last up to 50 years and will offer free
replacement for planks that may crack or splinter. While the initial
cost of plastic lumber may be hard to sell to owners, the long-term
effect can be emphasized as a money saver. |
|
|
|
|
|
|
|
|
|
|
|
|
|