2024
|
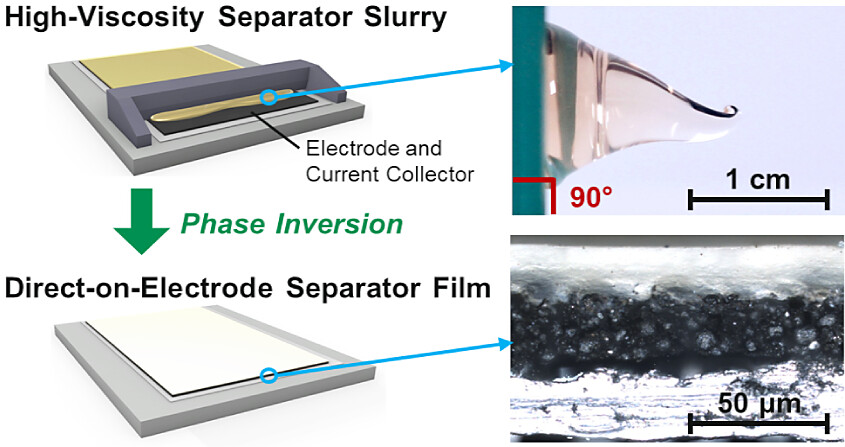 | Katz, Michelle E. R.; Cobb, Corie L. High-Viscosity Phase Inversion Separators for Freestanding and Direct-on-Electrode Manufacturing in Lithium-Ion Batteries Journal Article In: ACS Applied Materials & Interfaces, vol. 16, no. 34, pp. 44863–44878, 2024, ISSN: 1944-8244, (Publisher: American Chemical Society). @article{katz_high-viscosity_2024,
title = {High-Viscosity Phase Inversion Separators for Freestanding and Direct-on-Electrode Manufacturing in Lithium-Ion Batteries},
author = {Michelle E. R. Katz and Corie L. Cobb},
url = {https://doi.org/10.1021/acsami.4c09342},
doi = {10.1021/acsami.4c09342},
issn = {1944-8244},
year = {2024},
date = {2024-08-28},
urldate = {2024-08-28},
journal = {ACS Applied Materials & Interfaces},
volume = {16},
number = {34},
pages = {44863–44878},
abstract = {Separators play a critical role in lithium-ion batteries (LIBs) by facilitating lithium-ion (Li-ion) transport while enabling safe battery operation. However, commercial separators made from polypropylene (PP) or polyethylene (PE) impose a discrete processing step in current LIB manufacturing as they cannot be manufactured with the same slot-die coating process used to fabricate the electrodes. Moreover, commercial separators cannot accommodate newer manufacturing processes used to produce leading-edge microbatteries and flexible batteries with customized form factors. As a path toward rethinking LIB fabrication, we have developed a high-viscosity polymer composite separator slurry that enables the fabrication of both freestanding and direct-on-electrode films. A streamlined phase inversion process is used to impart porosity in cast separator films upon drying. To understand the impacts of material composition and rheology on phase inversion processing and separator performance, we investigated four different separator formulations. We used either diethylene glycol (DEG) or triethyl phosphate (TEP) as a nonsolvent, and either silica (SiO2) or alumina (Al2O3) as an inorganic additive in a polyvinylidene fluoride-co-hexafluoropropylene (PVDF-HFP) matrix. Through a down-selection process, we developed a TEP-SiO2 separator formulation that matched or outperformed a commercial Celgard 2325 (PP/PE/PP) separator and a Beyond Battery ceramic-coated PE (CC/PE/CC) separator under rate and cycle life tests in LiFePO4textbarLi4Ti5O12 (LFPtextbarLTO) and LiNi0.5Mn0.3Co0.2O2textbargraphite (NMC-532textbargraphite) coin cells at C/10–1C rates. Our TEP-SiO2 slurry had a viscosity of 298 Pa s at a 1 s–1 shear rate and shear-thinning behavior. When deposited directly onto an LTO anode and cycled against an LFP cathode, the direct-on-electrode TEP-SiO2 separator increased the specific capacity by 58% and 304% at 2C rates relative to the PP/PE/PP and CC/PE/CC separators, respectively. Additionally, the freestanding TEP-SiO2 separator maintained dimensional stability when heated to 200 °C for 1 h and demonstrated a higher elastic modulus and hardness than the PP/PE/PP and CC/PE/CC separators when measured with nanoindentation.},
note = {Publisher: American Chemical Society},
keywords = {additive manufacturing, batteries, printed batteries},
pubstate = {published},
tppubtype = {article}
}
Separators play a critical role in lithium-ion batteries (LIBs) by facilitating lithium-ion (Li-ion) transport while enabling safe battery operation. However, commercial separators made from polypropylene (PP) or polyethylene (PE) impose a discrete processing step in current LIB manufacturing as they cannot be manufactured with the same slot-die coating process used to fabricate the electrodes. Moreover, commercial separators cannot accommodate newer manufacturing processes used to produce leading-edge microbatteries and flexible batteries with customized form factors. As a path toward rethinking LIB fabrication, we have developed a high-viscosity polymer composite separator slurry that enables the fabrication of both freestanding and direct-on-electrode films. A streamlined phase inversion process is used to impart porosity in cast separator films upon drying. To understand the impacts of material composition and rheology on phase inversion processing and separator performance, we investigated four different separator formulations. We used either diethylene glycol (DEG) or triethyl phosphate (TEP) as a nonsolvent, and either silica (SiO2) or alumina (Al2O3) as an inorganic additive in a polyvinylidene fluoride-co-hexafluoropropylene (PVDF-HFP) matrix. Through a down-selection process, we developed a TEP-SiO2 separator formulation that matched or outperformed a commercial Celgard 2325 (PP/PE/PP) separator and a Beyond Battery ceramic-coated PE (CC/PE/CC) separator under rate and cycle life tests in LiFePO4textbarLi4Ti5O12 (LFPtextbarLTO) and LiNi0.5Mn0.3Co0.2O2textbargraphite (NMC-532textbargraphite) coin cells at C/10–1C rates. Our TEP-SiO2 slurry had a viscosity of 298 Pa s at a 1 s–1 shear rate and shear-thinning behavior. When deposited directly onto an LTO anode and cycled against an LFP cathode, the direct-on-electrode TEP-SiO2 separator increased the specific capacity by 58% and 304% at 2C rates relative to the PP/PE/PP and CC/PE/CC separators, respectively. Additionally, the freestanding TEP-SiO2 separator maintained dimensional stability when heated to 200 °C for 1 h and demonstrated a higher elastic modulus and hardness than the PP/PE/PP and CC/PE/CC separators when measured with nanoindentation. |
2023
|
 | Johnson, Keith E.; Montano, Brandon C.; Nambu, Kailino J.; Armstrong, Emilee N.; Cobb, Corie L.; Begley, Matthew R. Two-dimensional patterning of mesoscale fibers using acoustophoresis Journal Article In: Materials & Design, vol. 234, pp. 112328, 2023, ISSN: 0264-1275. @article{johnson_two-dimensional_2023,
title = {Two-dimensional patterning of mesoscale fibers using acoustophoresis},
author = {Keith E. Johnson and Brandon C. Montano and Kailino J. Nambu and Emilee N. Armstrong and Corie L. Cobb and Matthew R. Begley},
url = {https://www.sciencedirect.com/science/article/pii/S0264127523007438},
doi = {10.1016/j.matdes.2023.112328},
issn = {0264-1275},
year = {2023},
date = {2023-10-01},
urldate = {2023-10-01},
journal = {Materials & Design},
volume = {234},
pages = {112328},
abstract = {The performance of functional composites can rely critically on the arrangement of secondary phases; for example, patterned networks of conductive particles can impart anisotropic thermal, electric or ionic conductivity while preserving flexibility in the matrix. We demonstrate the use of standing acoustic waves to generate periodic patterns of short fibers. We extend the range of possible patterns with the first demonstration of both rectangular grids and arrays of octagons interspersed with rectangles. These newly demonstrated patterns are rationalized using theoretical models of acoustic forces and torques on fibers that account for two-dimensional spatial variations arising from applied acoustic fields. The models enable simulations of fiber motion, which are used to (i) map out final fiber positions as a function of initial position and orientation, and (ii) corroborate experiments visualizing fiber motion and final patterns. This approach provides a fast and accurate way to predict emergent fiber patterns as a function of excitation modality and fiber length. The theory and experiments clearly indicate strong coupling between the length of the fibers and the spacing of the acoustic nodes. This coupling is used to estimate reductions in percolation thresholds associated with the ratio of fiber length and acoustic wavelength.},
keywords = {acoustic focusing, acoustophoresis, periodic patterns},
pubstate = {published},
tppubtype = {article}
}
The performance of functional composites can rely critically on the arrangement of secondary phases; for example, patterned networks of conductive particles can impart anisotropic thermal, electric or ionic conductivity while preserving flexibility in the matrix. We demonstrate the use of standing acoustic waves to generate periodic patterns of short fibers. We extend the range of possible patterns with the first demonstration of both rectangular grids and arrays of octagons interspersed with rectangles. These newly demonstrated patterns are rationalized using theoretical models of acoustic forces and torques on fibers that account for two-dimensional spatial variations arising from applied acoustic fields. The models enable simulations of fiber motion, which are used to (i) map out final fiber positions as a function of initial position and orientation, and (ii) corroborate experiments visualizing fiber motion and final patterns. This approach provides a fast and accurate way to predict emergent fiber patterns as a function of excitation modality and fiber length. The theory and experiments clearly indicate strong coupling between the length of the fibers and the spacing of the acoustic nodes. This coupling is used to estimate reductions in percolation thresholds associated with the ratio of fiber length and acoustic wavelength. |
 | Cobb, Corie L.; Katz, Michelle E. R. Engineering advanced Lithium-ion batteries with additive manufacturing Book Chapter In: Li, Jianlin; Jin, Congrui (Ed.): Processing and Manufacturing of Electrodes for Lithium-Ion Batteries, pp. 129–168, IET Digital Library, 2023, ISBN: 9781839536694. @inbook{cobb_engineering_2023,
title = {Engineering advanced Lithium-ion batteries with additive manufacturing},
author = {Corie L. Cobb and Michelle E. R. Katz},
editor = {Jianlin Li and Congrui Jin},
url = {https://digital-library.theiet.org/content/books/10.1049/pbpo227e_ch6},
doi = {10.1049/PBPO227E_ch6},
isbn = {9781839536694},
year = {2023},
date = {2023-08-01},
urldate = {2023-08-01},
booktitle = {Processing and Manufacturing of Electrodes for Lithium-Ion Batteries},
pages = {129--168},
publisher = {IET Digital Library},
abstract = {Additive manufacturing (AM) enables the fabrication of complex shapes and formfactors that are inefficient or impossible to produce with traditional subtractive machining tools. AM emerged in the 1980s to enable the rapid creation of functional prototypes (also known as rapid prototyping). The first commercial implementation of AM was a stereolithography (SLA) system developed by 3D Systems in 1987, wherein a laser solidified thin layers of a photoactive polymer solution. In the early 1990s, fused deposition modeling (FDM), selective laser sintering, and other AM modalities began to emerge and have continued to grow in the decades since. Within the last ten years, AM has gained traction as an approach to fabricate Lithium-ion batteries (LIBs) because it enables (1) novel three-dimensional (3D) electrodes that optimize energy and power performance and (2) customizable battery shapes for integrated and mechanically robust batteries for portable device applications. As energy storage demands grow, so does the need for LIBs to come in a multitude of sizes, shapes, and materials that meet the needs of a given application. In this chapter, we review the main AM approaches that have been used to produce LIBs with a focus on FDM, direct-ink write (DIW), inkjet printing (IJP), aerosol jet printing (AJP), electrostatic spray deposition (ESD), stereolithography (SLA), and newer field-assisted (FA) methods.},
keywords = {3D printing, additive manufacturing, batteries},
pubstate = {published},
tppubtype = {inbook}
}
Additive manufacturing (AM) enables the fabrication of complex shapes and formfactors that are inefficient or impossible to produce with traditional subtractive machining tools. AM emerged in the 1980s to enable the rapid creation of functional prototypes (also known as rapid prototyping). The first commercial implementation of AM was a stereolithography (SLA) system developed by 3D Systems in 1987, wherein a laser solidified thin layers of a photoactive polymer solution. In the early 1990s, fused deposition modeling (FDM), selective laser sintering, and other AM modalities began to emerge and have continued to grow in the decades since. Within the last ten years, AM has gained traction as an approach to fabricate Lithium-ion batteries (LIBs) because it enables (1) novel three-dimensional (3D) electrodes that optimize energy and power performance and (2) customizable battery shapes for integrated and mechanically robust batteries for portable device applications. As energy storage demands grow, so does the need for LIBs to come in a multitude of sizes, shapes, and materials that meet the needs of a given application. In this chapter, we review the main AM approaches that have been used to produce LIBs with a focus on FDM, direct-ink write (DIW), inkjet printing (IJP), aerosol jet printing (AJP), electrostatic spray deposition (ESD), stereolithography (SLA), and newer field-assisted (FA) methods. |
 | Johnson, Keith E.; Melchert, Drew S.; Armstrong, Emilee N.; Gianola, Daniel S.; Cobb, Corie L.; Begley, Matthew R. A simple, validated approach for design of two-dimensional periodic particle patterns via acoustophoresis Journal Article In: Materials & Design, pp. 112165, 2023, ISSN: 0264-1275. @article{johnson_simple_2023,
title = {A simple, validated approach for design of two-dimensional periodic particle patterns via acoustophoresis},
author = {Keith E. Johnson and Drew S. Melchert and Emilee N. Armstrong and Daniel S. Gianola and Corie L. Cobb and Matthew R. Begley},
url = {https://www.sciencedirect.com/science/article/pii/S0264127523005804},
doi = {10.1016/j.matdes.2023.112165},
issn = {0264-1275},
year = {2023},
date = {2023-07-20},
urldate = {2023-07-01},
journal = {Materials & Design},
pages = {112165},
abstract = {Two-dimensional patterning of microparticles enables a wide range of functional materials, including patterned energy storage electrodes, flexible electronics, and sensor arrays. Particle patterning via acoustics offers an attractive path to generate a wide variety of 2D periodic patterns that introduce tailorable hierarchical porosity, useful for controlling surface area, transport distances, and other properties. This method is most effective with micron scale particles and patterns of tens to hundreds of microns. To enable systematic exploration of the broad design space for such patterns, this work develops a model of 2D and 3D assembly of particles at high loadings and validates the obtained patterns against both experiments and more computationally intensive modeling techniques. Using this simple model, connections are mapped between input parameters (like actuation conditions, particle volume fraction, material properties) and output geometrical features (like void size and shape, pattern connectivity, and surface area) so that they can be tailored to given applications. The utility of this simple model is illustrated by predicting and then experimentally demonstrating new hierarchical patterns resulting from multiple waves of different frequencies interacting. These multiscale patterns offer the potential to lift the limits on surface area, diffusion distances, and other features.},
keywords = {acoustic focusing, architechted materials, periodic patterns},
pubstate = {published},
tppubtype = {article}
}
Two-dimensional patterning of microparticles enables a wide range of functional materials, including patterned energy storage electrodes, flexible electronics, and sensor arrays. Particle patterning via acoustics offers an attractive path to generate a wide variety of 2D periodic patterns that introduce tailorable hierarchical porosity, useful for controlling surface area, transport distances, and other properties. This method is most effective with micron scale particles and patterns of tens to hundreds of microns. To enable systematic exploration of the broad design space for such patterns, this work develops a model of 2D and 3D assembly of particles at high loadings and validates the obtained patterns against both experiments and more computationally intensive modeling techniques. Using this simple model, connections are mapped between input parameters (like actuation conditions, particle volume fraction, material properties) and output geometrical features (like void size and shape, pattern connectivity, and surface area) so that they can be tailored to given applications. The utility of this simple model is illustrated by predicting and then experimentally demonstrating new hierarchical patterns resulting from multiple waves of different frequencies interacting. These multiscale patterns offer the potential to lift the limits on surface area, diffusion distances, and other features. |
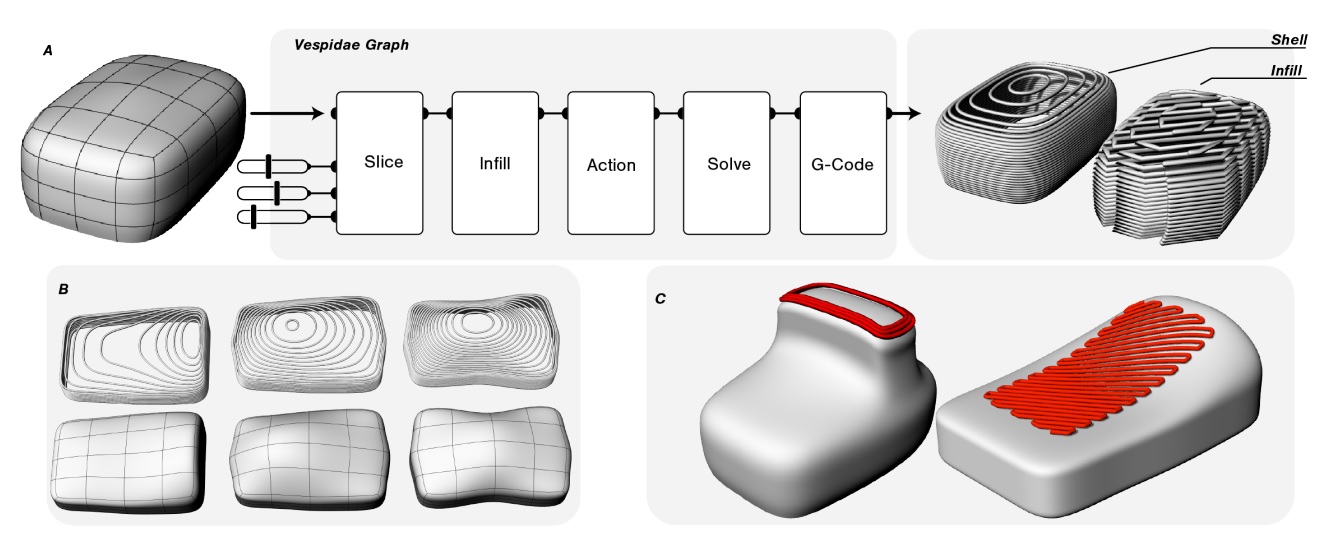 | Fossdal, Frikk H; Nguyen, Vinh; Heldal, Rogardt; Cobb, Corie L.; Peek, Nadya Vespidae: A Programming Framework for Developing Digital Fabrication Workflows Proceedings Article In: Proceedings of the 2023 ACM Designing Interactive Systems Conference, pp. 2034–2049, Association for Computing Machinery, New York, NY, USA, 2023, ISBN: 978-1-4503-9893-0. @inproceedings{fossdal_vespidae_2023,
title = {Vespidae: A Programming Framework for Developing Digital Fabrication Workflows},
author = {Frikk H Fossdal and Vinh Nguyen and Rogardt Heldal and Corie L. Cobb and Nadya Peek},
url = {https://dl.acm.org/doi/10.1145/3563657.3596106},
doi = {10.1145/3563657.3596106},
isbn = {978-1-4503-9893-0},
year = {2023},
date = {2023-07-01},
urldate = {2023-07-01},
booktitle = {Proceedings of the 2023 ACM Designing Interactive Systems Conference},
pages = {2034--2049},
publisher = {Association for Computing Machinery},
address = {New York, NY, USA},
series = {DIS '23},
abstract = {Digital fabrication machines are controlled through code. Software that generates this code, such as slicers, often rely on abstractions that restrict practitioners from exploring the full design space. We contribute Vespidae, a programming framework for developing custom toolpaths and visualizations. Vespidae module types include Toolpaths, Actions, Solvers, and Export. These generate geometry, specify machine tasks, sort and visualize action sequences, and generate and stream machine code. We show example workflows that demonstrate Vespidae’s strengths in supporting iteration and unconventional practice. These include non-planar 3D printing, varying a print’s tactile qualities with under-extrusion, and exploring the design space of milling marks. Furthermore, we used Vespidae over the course of six months to explore multi-material 3D printing for energy storage devices on a custom machine. Finally, we discuss how Vespidae contributes to a movement in HCI arguing for human-machine collaboration.},
keywords = {3D printing, CAD/CAM, Digital Fabrication},
pubstate = {published},
tppubtype = {inproceedings}
}
Digital fabrication machines are controlled through code. Software that generates this code, such as slicers, often rely on abstractions that restrict practitioners from exploring the full design space. We contribute Vespidae, a programming framework for developing custom toolpaths and visualizations. Vespidae module types include Toolpaths, Actions, Solvers, and Export. These generate geometry, specify machine tasks, sort and visualize action sequences, and generate and stream machine code. We show example workflows that demonstrate Vespidae’s strengths in supporting iteration and unconventional practice. These include non-planar 3D printing, varying a print’s tactile qualities with under-extrusion, and exploring the design space of milling marks. Furthermore, we used Vespidae over the course of six months to explore multi-material 3D printing for energy storage devices on a custom machine. Finally, we discuss how Vespidae contributes to a movement in HCI arguing for human-machine collaboration. |
2022
|
 | Hung, Chih-Hsuan; Huynh, Phong; Teo, Katrina; Cobb, Corie L. Are Three-Dimensional Batteries Beneficial? Analyzing Historical Data to Elucidate Performance Advantages Journal Article In: ACS Energy Letters, pp. 296-305, 2022. @article{hung_are_2022,
title = {Are Three-Dimensional Batteries Beneficial? Analyzing Historical Data to Elucidate Performance Advantages},
author = { Chih-Hsuan Hung and Phong Huynh and Katrina Teo and Corie L. Cobb},
url = {https://doi.org/10.1021/acsenergylett.2c02208},
doi = {10.1021/acsenergylett.2c02208},
year = {2022},
date = {2022-11-01},
urldate = {2022-11-01},
journal = {ACS Energy Letters},
pages = {296-305},
abstract = {Conventional lithium-ion batteries (LIBs) are composed of planar stacks of anodes, cathodes, and separators, all immersed in electrolyte and sandwiched between current collectors. However, planar LIBs have a performance trade-off where increasing electrode thickness leads to higher capacity but lower rate capability. Three-dimensional (3D) batteries circumvent this issue with 3D electrode architecture. Herein, we systematically analyze 3D LIBs from experimental publications over the past 20 years. Using a previously developed empirical model, we obtain parameters to quantify the rate capability and rate-limiting mechanisms of 3D LIBs. Compared to conventional LIBs, 3D LIBs exhibit better rate capability, confirming their expected performance benefit. To provide further insight, we investigate the impact of liquid-phase and solid-phase diffusion mechanisms on this performance benefit. Lastly, we discuss the design landscape of 3D LIBs across multiple electrode designs and material sets and highlight our perspective on the applicability of 3D LIBs at different application scales.},
keywords = {},
pubstate = {published},
tppubtype = {article}
}
Conventional lithium-ion batteries (LIBs) are composed of planar stacks of anodes, cathodes, and separators, all immersed in electrolyte and sandwiched between current collectors. However, planar LIBs have a performance trade-off where increasing electrode thickness leads to higher capacity but lower rate capability. Three-dimensional (3D) batteries circumvent this issue with 3D electrode architecture. Herein, we systematically analyze 3D LIBs from experimental publications over the past 20 years. Using a previously developed empirical model, we obtain parameters to quantify the rate capability and rate-limiting mechanisms of 3D LIBs. Compared to conventional LIBs, 3D LIBs exhibit better rate capability, confirming their expected performance benefit. To provide further insight, we investigate the impact of liquid-phase and solid-phase diffusion mechanisms on this performance benefit. Lastly, we discuss the design landscape of 3D LIBs across multiple electrode designs and material sets and highlight our perspective on the applicability of 3D LIBs at different application scales. |
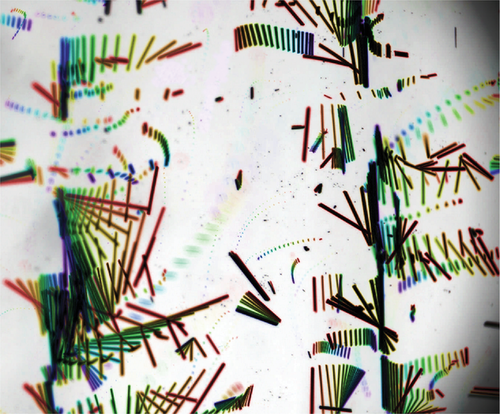 | Melchert, Drew S.; Tahmasebipour, Amir; Liu, Xin; Mancini, Julie; Moran, Bryan; Giera, Brian; Joshipura, Ishan D.; Shusteff, Maxim; Meinhart, Carl D.; Cobb, Corie L.; Spadaccini, Christopher; Gianola, Daniel S.; Begley, Matthew R. Anisotropic Thermally Conductive Composites Enabled by Acoustophoresis and Stereolithography Journal Article In: Advanced Functional Materials, pp. 2201687, 2022, ISSN: 1616-3028. @article{melchert_anisotropic_nodate,
title = {Anisotropic Thermally Conductive Composites Enabled by Acoustophoresis and Stereolithography},
author = {Drew S. Melchert and Amir Tahmasebipour and Xin Liu and Julie Mancini and Bryan Moran and Brian Giera and Ishan D. Joshipura and Maxim Shusteff and Carl D. Meinhart and Corie L. Cobb and Christopher Spadaccini and Daniel S. Gianola and Matthew R. Begley},
url = {https://onlinelibrary.wiley.com/doi/abs/10.1002/adfm.202201687},
doi = {10.1002/adfm.202201687},
issn = {1616-3028},
year = {2022},
date = {2022-05-17},
urldate = {2022-05-17},
journal = {Advanced Functional Materials},
pages = {2201687},
abstract = {Opportunities to improve thermal management in electronic devices are currently hindered by processing constraints that limit thermal conductivity in polymer-matrix composites. Active patterning of filler particles is a promising route to improve conductivity while retaining processability by improving particle contact density and directing heat along optimized pathways. This study employs acoustic patterning to align and compact filler particles into stripes during stereolithographic 3D printing. This approach produces polymer-based composite materials with highly efficient embedded heat transport pathways which reach 95 vol% particle utilization (relative to the parallel conduction upper limit). These composites exhibit anisotropic thermal conductivity up to 300% higher than unpatterned composites, with in-plane anisotropy ratios of up to 350%. Combining this high conductivity with 3D printing enables materials with engineered heat networks that optimize transport from hot spots to heatsinks while maintaining low viscosity for fast particle patterning and for infiltration around electronic components. Finally, numerical simulations of acoustic assembly of particles with varied geometry, when compared to experimentally characterized particle packing, illuminate pathways for further improving conductivity by optimizing particle geometry for alignment and stacking of particles with maximum contact surface area.},
keywords = {3D printing, acoustophoresis, composites, stereolithography},
pubstate = {published},
tppubtype = {article}
}
Opportunities to improve thermal management in electronic devices are currently hindered by processing constraints that limit thermal conductivity in polymer-matrix composites. Active patterning of filler particles is a promising route to improve conductivity while retaining processability by improving particle contact density and directing heat along optimized pathways. This study employs acoustic patterning to align and compact filler particles into stripes during stereolithographic 3D printing. This approach produces polymer-based composite materials with highly efficient embedded heat transport pathways which reach 95 vol% particle utilization (relative to the parallel conduction upper limit). These composites exhibit anisotropic thermal conductivity up to 300% higher than unpatterned composites, with in-plane anisotropy ratios of up to 350%. Combining this high conductivity with 3D printing enables materials with engineered heat networks that optimize transport from hot spots to heatsinks while maintaining low viscosity for fast particle patterning and for infiltration around electronic components. Finally, numerical simulations of acoustic assembly of particles with varied geometry, when compared to experimentally characterized particle packing, illuminate pathways for further improving conductivity by optimizing particle geometry for alignment and stacking of particles with maximum contact surface area. |
2021
|
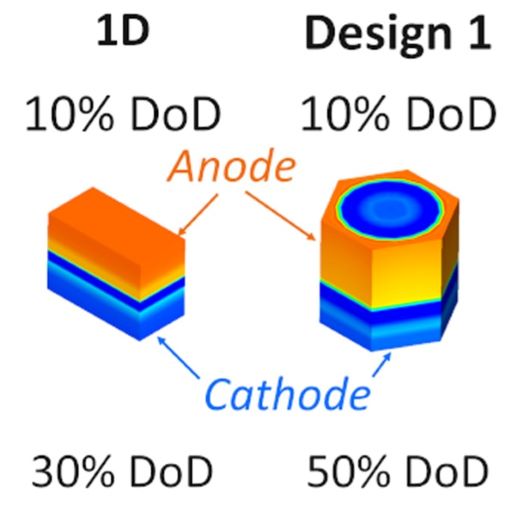 | Hung, Chih-Hsuan; Allu, Srikanth; Cobb, Corie L Modeling Current Density Non-Uniformities to Understand High-Rate Limitations in 3D Interdigitated Lithium-ion Batteries Journal Article In: Journal of The Electrochemical Society, vol. 168, no. 10, pp. 100512, 2021, ISSN: 1945-7111, (Publisher: The Electrochemical Society). @article{hung_modeling_2021,
title = {Modeling Current Density Non-Uniformities to Understand High-Rate Limitations in 3D Interdigitated Lithium-ion Batteries},
author = {Chih-Hsuan Hung and Srikanth Allu and Corie L Cobb},
url = {https://doi.org/10.1149/1945-7111/ac2ac5},
doi = {10.1149/1945-7111/ac2ac5},
issn = {1945-7111},
year = {2021},
date = {2021-10-08},
urldate = {2021-10-08},
journal = {Journal of The Electrochemical Society},
volume = {168},
number = {10},
pages = {100512},
abstract = {Conventional planar Lithium-ion battery (LIB) cells are composed of a cathode and an anode with a polymer separator sheet sandwiched in between. Three-dimensional (3D) interdigitated batteries, where an anode and a cathode are intertwined, have been proposed as an alternative to planar LIBs to significantly improve energy, power, and fast charge performance. Various 3D battery designs have been demonstrated by researchers over the years, but a systematic study of how architecture and material impact 3D battery performance has been limited. In this paper, we conduct a comparative 3D computational modeling study on four 3D interdigitated battery designs previously shown in literature. We model each 3D battery using Li4Ti5O12 (LTO)∣LiFePO4 (LFP) and Graphite∣LiNi0.5Mn0.3Co0.2O2 (NMC), two widely studied LIB material systems, while conserving mass across all designs. Moreover, we propose a 3D current density metric to evaluate 3D LIBs and quantify the impact of current non-uniformities on high-rate LIB performance. Our results indicate that material selection and 3D architecture are equally critical for maximizing performance at high discharge rates. In addition, our analysis suggests quantifying the rate of change in current density early in a model discharge cycle can be a guiding metric to screen designs more quickly for premature failure.},
note = {Publisher: The Electrochemical Society},
keywords = {additive manufacturing, battery modeling},
pubstate = {published},
tppubtype = {article}
}
Conventional planar Lithium-ion battery (LIB) cells are composed of a cathode and an anode with a polymer separator sheet sandwiched in between. Three-dimensional (3D) interdigitated batteries, where an anode and a cathode are intertwined, have been proposed as an alternative to planar LIBs to significantly improve energy, power, and fast charge performance. Various 3D battery designs have been demonstrated by researchers over the years, but a systematic study of how architecture and material impact 3D battery performance has been limited. In this paper, we conduct a comparative 3D computational modeling study on four 3D interdigitated battery designs previously shown in literature. We model each 3D battery using Li4Ti5O12 (LTO)∣LiFePO4 (LFP) and Graphite∣LiNi0.5Mn0.3Co0.2O2 (NMC), two widely studied LIB material systems, while conserving mass across all designs. Moreover, we propose a 3D current density metric to evaluate 3D LIBs and quantify the impact of current non-uniformities on high-rate LIB performance. Our results indicate that material selection and 3D architecture are equally critical for maximizing performance at high discharge rates. In addition, our analysis suggests quantifying the rate of change in current density early in a model discharge cycle can be a guiding metric to screen designs more quickly for premature failure. |
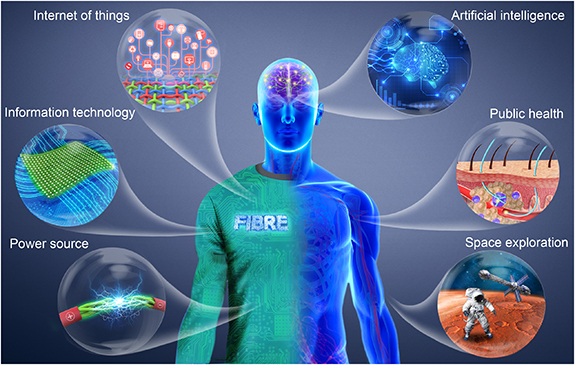 | Bonnassieux, Yvan; Brabec, Christoph J; Cao, Yong; Carmichael, Tricia Breen; Chabinyc, Michael L; Cheng, Kwang-Ting; Cho, Gyoujin; Chung, Anjung; Cobb, Corie L; Distler, Andreas; Egelhaaf, Hans-Joachim; Grau, Gerd; Guo, Xiaojun; Haghiashtiani, Ghazaleh; Huang, Tsung-Ching; Hussain, Muhammad M; Iniguez, Benjamin; Lee, Taik-Min; Li, Ling; Ma, Yuguang; Ma, Dongge; McAlpine, Michael C; Ng, Tse Nga; Österbacka, Ronald; Patel, Shrayesh N; Peng, Junbiao; Peng, Huisheng; Rivnay, Jonathan; Shao, Leilai; Steingart, Daniel; Street, Robert A; Subramanian, Vivek; Torsi, Luisa; Wu, Yunyun The 2021 flexible and printed electronics roadmap Journal Article In: Flexible and Printed Electronics, vol. 6, no. 2, pp. 023001, 2021, ISSN: 2058-8585, (Publisher: IOP Publishing). @article{bonnassieux_2021,
title = {The 2021 flexible and printed electronics roadmap},
author = {Yvan Bonnassieux and Christoph J Brabec and Yong Cao and Tricia Breen Carmichael and Michael L Chabinyc and Kwang-Ting Cheng and Gyoujin Cho and Anjung Chung and Corie L Cobb and Andreas Distler and Hans-Joachim Egelhaaf and Gerd Grau and Xiaojun Guo and Ghazaleh Haghiashtiani and Tsung-Ching Huang and Muhammad M Hussain and Benjamin Iniguez and Taik-Min Lee and Ling Li and Yuguang Ma and Dongge Ma and Michael C McAlpine and Tse Nga Ng and Ronald Österbacka and Shrayesh N Patel and Junbiao Peng and Huisheng Peng and Jonathan Rivnay and Leilai Shao and Daniel Steingart and Robert A Street and Vivek Subramanian and Luisa Torsi and Yunyun Wu},
url = {https://doi.org/10.1088/2058-8585/abf986},
doi = {10.1088/2058-8585/abf986},
issn = {2058-8585},
year = {2021},
date = {2021-05-17},
urldate = {2021-05-17},
journal = {Flexible and Printed Electronics},
volume = {6},
number = {2},
pages = {023001},
abstract = {This roadmap includes the perspectives and visions of leading researchers in the key areas of flexible and printable electronics. The covered topics are broadly organized by the device technologies (sections 1–9), fabrication techniques (sections 10–12), and design and modeling approaches (sections 13 and 14) essential to the future development of new applications leveraging flexible electronics (FE). The interdisciplinary nature of this field involves everything from fundamental scientific discoveries to engineering challenges; from design and synthesis of new materials via novel device design to modelling and digital manufacturing of integrated systems. As such, this roadmap aims to serve as a resource on the current status and future challenges in the areas covered by the roadmap and to highlight the breadth and wide-ranging opportunities made available by FE technologies.},
note = {Publisher: IOP Publishing},
keywords = {printed electronics, wearables},
pubstate = {published},
tppubtype = {article}
}
This roadmap includes the perspectives and visions of leading researchers in the key areas of flexible and printable electronics. The covered topics are broadly organized by the device technologies (sections 1–9), fabrication techniques (sections 10–12), and design and modeling approaches (sections 13 and 14) essential to the future development of new applications leveraging flexible electronics (FE). The interdisciplinary nature of this field involves everything from fundamental scientific discoveries to engineering challenges; from design and synthesis of new materials via novel device design to modelling and digital manufacturing of integrated systems. As such, this roadmap aims to serve as a resource on the current status and future challenges in the areas covered by the roadmap and to highlight the breadth and wide-ranging opportunities made available by FE technologies. |
 | Melchert, Drew S; Johnson, Keith; Giera, Brian; Fong, Erika J; Shusteff, Maxim; Mancini, Julie; Karnes, John J; Cobb, Corie L; Spadaccini, Christopher; Gianola, Daniel S; Begley, Matthew R Modeling meso- and microstructure in materials patterned with acoustic focusing Journal Article In: Materials & Design, pp. 109512, 2021, ISSN: 0264-1275. @article{melchert_modeling_2021,
title = {Modeling meso- and microstructure in materials patterned with acoustic focusing},
author = {Drew S Melchert and Keith Johnson and Brian Giera and Erika J Fong and Maxim Shusteff and Julie Mancini and John J Karnes and Corie L Cobb and Christopher Spadaccini and Daniel S Gianola and Matthew R Begley},
url = {http://www.sciencedirect.com/science/article/pii/S0264127521000654},
doi = {10.1016/j.matdes.2021.109512},
issn = {0264-1275},
year = {2021},
date = {2021-01-26},
urldate = {2021-01-28},
journal = {Materials & Design},
pages = {109512},
abstract = {We conduct numerical simulations of acoustic focusing in dense suspensions to map the design space of acoustically patterned materials. We develop closed-form expressions for acoustic forces on particles, enabling rapid simulation of thousands of particles, and find excellent agreement with experimentally focused patterns over a range of conditions. We map the geometrical and microstructural features of focused particle patterns and their dependence on processing parameters. We find that mesostructural geometrical features (focused line height, width, and profile shape) can be controlled reliably over a broad range by modulating input parameters, and that while microstructural features are less readily modulated via input parameters, they are well-suited for various transport properties in functional materials. Notably, packing density nears the random close packing limit at 0.64, and particle contact density shows anisotropy favoring particle contacts along the focused lines. These results guide process design for controlling the properties of patterned materials, and outline the property ranges accessible via acoustic focusing. Additionally, we discuss the dependence of material functionalities, particularly electrical, thermal, and ionic transport properties, on the meso- and micro-structural features of patterned composite materials in the context of acoustic focusing.},
keywords = {additive manufacturing, architected materials, composite materials},
pubstate = {published},
tppubtype = {article}
}
We conduct numerical simulations of acoustic focusing in dense suspensions to map the design space of acoustically patterned materials. We develop closed-form expressions for acoustic forces on particles, enabling rapid simulation of thousands of particles, and find excellent agreement with experimentally focused patterns over a range of conditions. We map the geometrical and microstructural features of focused particle patterns and their dependence on processing parameters. We find that mesostructural geometrical features (focused line height, width, and profile shape) can be controlled reliably over a broad range by modulating input parameters, and that while microstructural features are less readily modulated via input parameters, they are well-suited for various transport properties in functional materials. Notably, packing density nears the random close packing limit at 0.64, and particle contact density shows anisotropy favoring particle contacts along the focused lines. These results guide process design for controlling the properties of patterned materials, and outline the property ranges accessible via acoustic focusing. Additionally, we discuss the dependence of material functionalities, particularly electrical, thermal, and ionic transport properties, on the meso- and micro-structural features of patterned composite materials in the context of acoustic focusing. |
2020
|
 | Johnson, David Mathew; Cobb, Corie Lynn; Paschkewitz, John Steven System for creating a structure including a vasculature network Patent 10,744,686, 2020. @patent{johnson_system_2020,
title = {System for creating a structure including a vasculature network},
author = {David Mathew Johnson and Corie Lynn Cobb and John Steven Paschkewitz},
url = {https://patents.google.com/patent/US10744686B2/en?oq=10%2c744%2c686},
year = {2020},
date = {2020-08-08},
urldate = {2020-12-15},
number = {10,744,686},
abstract = {A system and method is provided for creating a structure including a vasculature network. A film deposition device is configured to dispense droplets onto a surface of a substrate to form a curable fugitive pre-patterned liquid film on the surface of the substrate. An electrohydrodynamic film patterning (EHD-FP) device has a patterned electrode structure formed to generate an electric field and to subject the film on the surface of the substrate to the electric field. The film thereby being formed by the EHD-FP into patterned features in response to being subjected to the electric field. Then a casting system is configured to cover the patterned features in an epoxy to form patterned structures, wherein the patterned structures comprise a fugitive vasculature structure.},
keywords = {patterned},
pubstate = {published},
tppubtype = {patent}
}
A system and method is provided for creating a structure including a vasculature network. A film deposition device is configured to dispense droplets onto a surface of a substrate to form a curable fugitive pre-patterned liquid film on the surface of the substrate. An electrohydrodynamic film patterning (EHD-FP) device has a patterned electrode structure formed to generate an electric field and to subject the film on the surface of the substrate to the electric field. The film thereby being formed by the EHD-FP into patterned features in response to being subjected to the electric field. Then a casting system is configured to cover the patterned features in an epoxy to form patterned structures, wherein the patterned structures comprise a fugitive vasculature structure. |
 | de Lannoy, Charles-Francois; Cobb, Corie Lynn Membrane surface hydrophobicity through electro-hydrodynamic film patterning Patent 10,710,283, 2020. @patent{lannoy_membrane_2020,
title = {Membrane surface hydrophobicity through electro-hydrodynamic film patterning},
author = {Charles-Francois de Lannoy and Corie Lynn Cobb},
url = {https://patents.google.com/patent/US10710283B2/en?oq=10%2c710%2c283},
year = {2020},
date = {2020-07-14},
urldate = {2020-12-15},
number = {10,710,283},
abstract = {A roll-to-roll system for forming a hydrophobic polymer membrane surface includes a heated carrier belt, a repository of polymer material arranged to deposit the polymer material onto the carrier to create a heated polymer, an electrode belt positioned opposite the carrier belt, an electric field generator positioned to generate an electric field between the carrier belt and the electrode belt and to infuse a pattern into the heated polymer to form a patterned polymer film, and a solvent bath to rinse the patterned polymer film. A method of creating a hydrophobic polymer membrane surface includes depositing a polymer material onto a heated carrier, using the carrier, transporting the polymer material past an electrode that acts as an electric field generator, generating an electric field adjacent the carrier, using the electric field to infuse a pattern into the polymer membrane surface, and setting the pattern into the polymer membrane surface.},
keywords = {patterned},
pubstate = {published},
tppubtype = {patent}
}
A roll-to-roll system for forming a hydrophobic polymer membrane surface includes a heated carrier belt, a repository of polymer material arranged to deposit the polymer material onto the carrier to create a heated polymer, an electrode belt positioned opposite the carrier belt, an electric field generator positioned to generate an electric field between the carrier belt and the electrode belt and to infuse a pattern into the heated polymer to form a patterned polymer film, and a solvent bath to rinse the patterned polymer film. A method of creating a hydrophobic polymer membrane surface includes depositing a polymer material onto a heated carrier, using the carrier, transporting the polymer material past an electrode that acts as an electric field generator, generating an electric field adjacent the carrier, using the electric field to infuse a pattern into the polymer membrane surface, and setting the pattern into the polymer membrane surface. |
 | Hatzell, Kelsey B.; Chen, Xi Chelsea; Cobb, Corie L.; Dasgupta, Neil P; Dixit, Marm B.; Marbella, Lauren E; McDowell, Matthew T.; Mukherjee, Partha; Verma, Ankit; Viswanathan, Venkatasubramanian; Westover, Andrew; Zeier, Wolfgang G. Challenges in lithium metal anodes for solid state batteries Journal Article In: ACS Energy Letters, vol. 5, no. 3, pp. 922-934, 2020. @article{hatzell_challenges_2020,
title = {Challenges in lithium metal anodes for solid state batteries},
author = { Kelsey B. Hatzell and Xi Chelsea Chen and Corie L. Cobb and Neil P Dasgupta and Marm B. Dixit and Lauren E Marbella and Matthew T. McDowell and Partha Mukherjee and Ankit Verma and Venkatasubramanian Viswanathan and Andrew Westover and Wolfgang G. Zeier},
url = {https://doi.org/10.1021/acsenergylett.9b02668},
doi = {10.1021/acsenergylett.9b02668},
year = {2020},
date = {2020-02-18},
urldate = {2020-02-18},
journal = {ACS Energy Letters},
volume = {5},
number = {3},
pages = {922-934},
abstract = {In this perspective, we highlight recent progress and challenges related to the integration of lithium metal anodes in solid-state batteries. While prior reports have suggested that solid electrolytes may be impermeable to lithium metal, this hypothesis has been disproven under a variety of electrolyte compositions and cycling conditions. Herein, we describe the mechanistic origins and importance of lithium filament growth and interphase formation in inorganic and organic solid electrolytes. Multi-modal techniques that combine real and reciprocal space imaging and modeling will be necessary to fully understand non-equilibrium dynamics at these buried interfaces. Currently, most studies on lithium electrode kinetics at solid electrolyte interfaces are completed in symmetric Li-Li configurations. To fully understand the challenges and opportunities afforded by Li metal anodes, full-cell experiments are necessary. Finally, the impacts of operating conditions on solid state batteries are largely unknown with respect to pressure, geometry, and break-in protocols. Given the rapid growth of this community and diverse portfolio of solid electrolytes, we highlight the need for detailed reporting of experimental conditions and standardization of protocols across the community.},
keywords = {batteries},
pubstate = {published},
tppubtype = {article}
}
In this perspective, we highlight recent progress and challenges related to the integration of lithium metal anodes in solid-state batteries. While prior reports have suggested that solid electrolytes may be impermeable to lithium metal, this hypothesis has been disproven under a variety of electrolyte compositions and cycling conditions. Herein, we describe the mechanistic origins and importance of lithium filament growth and interphase formation in inorganic and organic solid electrolytes. Multi-modal techniques that combine real and reciprocal space imaging and modeling will be necessary to fully understand non-equilibrium dynamics at these buried interfaces. Currently, most studies on lithium electrode kinetics at solid electrolyte interfaces are completed in symmetric Li-Li configurations. To fully understand the challenges and opportunities afforded by Li metal anodes, full-cell experiments are necessary. Finally, the impacts of operating conditions on solid state batteries are largely unknown with respect to pressure, geometry, and break-in protocols. Given the rapid growth of this community and diverse portfolio of solid electrolytes, we highlight the need for detailed reporting of experimental conditions and standardization of protocols across the community. |
2019
|
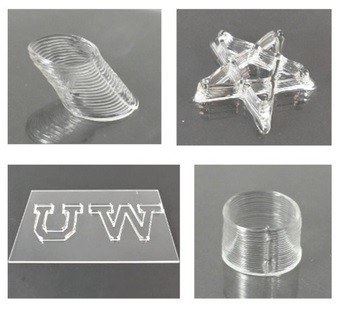 | Wong, Jitkanya; Gong, Alex T.; Defnet, Peter A.; Meabe, Leire; Beauchamp, Bruce; Sweet, Robert M.; Sardon, Haritz; Cobb, Corie L.; Nelson, Alshakim 3D Printing Ionogel Auxetic Frameworks for Stretchable Sensors Journal Article In: Advanced Materials Technologies, vol. 4, no. 9, pp. 1900452, 2019. @article{doi:10.1002/admt.201900452,
title = {3D Printing Ionogel Auxetic Frameworks for Stretchable Sensors},
author = { Jitkanya Wong and Alex T. Gong and Peter A. Defnet and Leire Meabe and Bruce Beauchamp and Robert M. Sweet and Haritz Sardon and Corie L. Cobb and Alshakim Nelson},
url = {https://onlinelibrary.wiley.com/doi/abs/10.1002/admt.201900452},
doi = {10.1002/admt.201900452},
year = {2019},
date = {2019-08-08},
urldate = {2019-08-08},
journal = {Advanced Materials Technologies},
volume = {4},
number = {9},
pages = {1900452},
abstract = {Ionogels are an emerging class of soft materials that exhibit ionic conductivity and thermal stability without the need to replenish ions or the addition of conductive particle fillers. An ionogel ink is reported for direct-write 3D printing to fabricate conductive structures that can vary in the printed object geometries. This approach relies on a shear-thinning ionogel ink that can be extruded to afford self-supporting constructs. After a brief UV cure, the printed construct is transformed into a mechanically tough, transparent structure that is ionically conductive. Upon application of stretching and twisting loads, the 3D-printed objects exhibit detectable changes in conductivity. To demonstrate the versatility of rapid prototyping with the ionogel inks, an auxetic structure is 3D printed and tested as a strain sensor. The printed auxetic structure exhibits an electrical response to strain, but also demonstrates increased extensibility and operational range in comparison to a casted bulk film with the same outer dimensions.},
keywords = {},
pubstate = {published},
tppubtype = {article}
}
Ionogels are an emerging class of soft materials that exhibit ionic conductivity and thermal stability without the need to replenish ions or the addition of conductive particle fillers. An ionogel ink is reported for direct-write 3D printing to fabricate conductive structures that can vary in the printed object geometries. This approach relies on a shear-thinning ionogel ink that can be extruded to afford self-supporting constructs. After a brief UV cure, the printed construct is transformed into a mechanically tough, transparent structure that is ionically conductive. Upon application of stretching and twisting loads, the 3D-printed objects exhibit detectable changes in conductivity. To demonstrate the versatility of rapid prototyping with the ionogel inks, an auxetic structure is 3D printed and tested as a strain sensor. The printed auxetic structure exhibits an electrical response to strain, but also demonstrates increased extensibility and operational range in comparison to a casted bulk film with the same outer dimensions. |
2018
|
 | Johnson, David Mathew; Cobb, Corie Lynn; Paschkewitz, John Steven Integral vasculature Patent US9884437B2, 2018. @patent{johnson_integral_2018,
title = {Integral vasculature},
author = {David Mathew Johnson and Corie Lynn Cobb and John Steven Paschkewitz},
url = {https://patents.google.com/patent/US9884437B2/en},
year = {2018},
date = {2018-02-01},
urldate = {2018-03-05},
number = {US9884437B2},
abstract = {A system and method is provided for creating a structure including a vasculature network. A film deposition device is configured to dispense droplets onto a surface of a substrate to form a curable fugitive pre-patterned liquid film on the surface of the substrate. An electrohydrodynamic film patterning (EHD-FP) device has a patterned electrode structure formed to generate an electric field and to subject the film on the surface of the substrate to the electric field. The film thereby being formed by the EHD-FP into patterned features in response to being subjected to the electric field. Then a casting system is configured to cover the patterned features in an epoxy to form patterned structures, wherein the patterned structures comprise a fugitive vasculature structure.},
keywords = {additive manufacturing, composite materials},
pubstate = {published},
tppubtype = {patent}
}
A system and method is provided for creating a structure including a vasculature network. A film deposition device is configured to dispense droplets onto a surface of a substrate to form a curable fugitive pre-patterned liquid film on the surface of the substrate. An electrohydrodynamic film patterning (EHD-FP) device has a patterned electrode structure formed to generate an electric field and to subject the film on the surface of the substrate to the electric field. The film thereby being formed by the EHD-FP into patterned features in response to being subjected to the electric field. Then a casting system is configured to cover the patterned features in an epoxy to form patterned structures, wherein the patterned structures comprise a fugitive vasculature structure. |
 | Cobb, Corie Lynn Structures for interdigitated finger co-extrusion Patent US9899669B2, 2018. @patent{cobb_structures_2018,
title = {Structures for interdigitated finger co-extrusion},
author = {Corie Lynn Cobb},
url = {https://patents.google.com/patent/US9899669B2/en},
year = {2018},
date = {2018-02-01},
urldate = {2018-03-14},
number = {US9899669B2},
abstract = {An electrode structure has an interdigitated layer of at least a first material and a second material, the second material having either higher or similar electrical conductivity of the first material and being more ionically conductivity than the first material, a cross-section of the two materials being non-rectangular.},
keywords = {additive manufacturing, Co-extrusion, printed batteries},
pubstate = {published},
tppubtype = {patent}
}
An electrode structure has an interdigitated layer of at least a first material and a second material, the second material having either higher or similar electrical conductivity of the first material and being more ionically conductivity than the first material, a cross-section of the two materials being non-rectangular. |
 | Cobb, Corie Lynn Co-extrusion print head with edge bead reduction Patent US9855578B2, 2018. @patent{cobb_co-extrusion_2018,
title = {Co-extrusion print head with edge bead reduction},
author = {Corie Lynn Cobb},
url = {https://patents.google.com/patent/US9855578B2/en},
year = {2018},
date = {2018-01-01},
urldate = {2018-03-05},
number = {US9855578B2},
abstract = {A co-extrusion print head has at least one channel, and a set of orifices fluidically connected to the channel, wherein the set of orifices has at least one orifice at each edge of the set has a smaller vertical extent than the other orifices.},
keywords = {additive manufacturing, Co-extrusion, printed batteries},
pubstate = {published},
tppubtype = {patent}
}
A co-extrusion print head has at least one channel, and a set of orifices fluidically connected to the channel, wherein the set of orifices has at least one orifice at each edge of the set has a smaller vertical extent than the other orifices. |
2017
|
 | Cobb, Corie Lynn Co-extruded conformal battery separator and electrode Patent US9755221B2, 2017. @patent{cobb_co-extruded_2017,
title = {Co-extruded conformal battery separator and electrode},
author = {Corie Lynn Cobb},
url = {https://patents.google.com/patent/US9755221B2/en},
year = {2017},
date = {2017-09-01},
urldate = {2018-03-05},
number = {US9755221B2},
abstract = {A co-extrusion print head has at least one separator inlet port, at least a first, second and third series of channels arranged to receive a separator material from the separator inlet port, at least one electrode inlet port, a fourth series of channels arranged to receive an electrode material from the electrode inlet port, a first merge portion connected to the first, second, third and fourth series of channels, the merge portion positioned to receive and merge the separator material into a separator flow and the electrode material into an electrode flow, a second merge portion connected to the first merge portion, the second merge portion positioned to receive and merge the separator flows and the electrode flows, and an outlet port connected to the second merge portion, the outlet port arranged to deposit the separator and electrode materials from the merge portion as a stack on a substrate.},
keywords = {additive manufacturing, Co-extrusion, printed batteries},
pubstate = {published},
tppubtype = {patent}
}
A co-extrusion print head has at least one separator inlet port, at least a first, second and third series of channels arranged to receive a separator material from the separator inlet port, at least one electrode inlet port, a fourth series of channels arranged to receive an electrode material from the electrode inlet port, a first merge portion connected to the first, second, third and fourth series of channels, the merge portion positioned to receive and merge the separator material into a separator flow and the electrode material into an electrode flow, a second merge portion connected to the first merge portion, the second merge portion positioned to receive and merge the separator flows and the electrode flows, and an outlet port connected to the second merge portion, the outlet port arranged to deposit the separator and electrode materials from the merge portion as a stack on a substrate. |
 | Ng, Tse Nga; Mei, Ping; Cobb, Corie Lynn; Ready, Steven E; Paschkewitz, John S Structural designs for stretchable, conformal electrical interconnects Patent US20170215284A1, 2017. @patent{ng_structural_2017,
title = {Structural designs for stretchable, conformal electrical interconnects},
author = {Tse Nga Ng and Ping Mei and Corie Lynn Cobb and Steven E Ready and John S Paschkewitz},
url = {https://patents.google.com/patent/US20170215284A1/en?inventor=Corie+Lynn+Cobb&country=US&page=1},
year = {2017},
date = {2017-07-01},
urldate = {2018-03-13},
number = {US20170215284A1},
abstract = {Disclosed is a conformable, stretchable and electrical conductive structure, which includes an auxetic structure, and a plurality of electrical conductors. The plurality of electrical conductors being incorporated within the auxetic structure, to form conformable, stretchable electrical interconnects, configured based on a design of the auxetic structure and placement of the electrical conductors incorporated with the auxetic structure.},
keywords = {additive manufacturing, printed electronics},
pubstate = {published},
tppubtype = {patent}
}
Disclosed is a conformable, stretchable and electrical conductive structure, which includes an auxetic structure, and a plurality of electrical conductors. The plurality of electrical conductors being incorporated within the auxetic structure, to form conformable, stretchable electrical interconnects, configured based on a design of the auxetic structure and placement of the electrical conductors incorporated with the auxetic structure. |
 | Cobb, Corie Lynn; Bae, Chang-Jun Three dimensional co-extruded battery electrodes Patent US9590232B2, 2017. @patent{cobb_three_2017-1,
title = {Three dimensional co-extruded battery electrodes},
author = {Corie Lynn Cobb and Chang-Jun Bae},
url = {https://patents.google.com/patent/US9590232B2/en},
year = {2017},
date = {2017-03-01},
urldate = {2018-03-14},
number = {US9590232B2},
abstract = {A three dimensional electrode structure having a first layer of interdigitated stripes of material oriented in a first direction, and a second layer of interdigitated stripes of material oriented in a second direction residing on the first layer of interdigitated stripes of material. A method of manufacturing a three dimensional electrode structure includes depositing a first layer of interdigitated stripes of an active material and an intermediate material on a substrate in a first direction, and depositing a second layer of interdigitated stripes of the active material and the intermediate material on the first layer in a second direction orthogonal to the first direction.},
keywords = {additive manufacturing, Co-extrusion, printed batteries},
pubstate = {published},
tppubtype = {patent}
}
A three dimensional electrode structure having a first layer of interdigitated stripes of material oriented in a first direction, and a second layer of interdigitated stripes of material oriented in a second direction residing on the first layer of interdigitated stripes of material. A method of manufacturing a three dimensional electrode structure includes depositing a first layer of interdigitated stripes of an active material and an intermediate material on a substrate in a first direction, and depositing a second layer of interdigitated stripes of the active material and the intermediate material on the first layer in a second direction orthogonal to the first direction. |
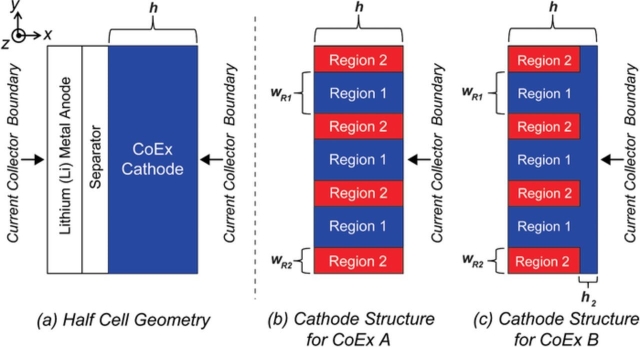 | Cobb, Corie L; Solberg, Scott E Communication—Analysis of Thick Co-Extruded Cathodes for Higher-Energy-and-Power Lithium-Ion Batteries Journal Article In: Journal of The Electrochemical Society, vol. 164, no. 7, pp. A1339–A1341, 2017, ISSN: 0013-4651, 1945-7111. @article{cobb_communicationanalysis_2017,
title = {Communication—Analysis of Thick Co-Extruded Cathodes for Higher-Energy-and-Power Lithium-Ion Batteries},
author = {Corie L Cobb and Scott E Solberg},
url = {https://iopscience.iop.org/article/10.1149/2.0101707jes},
doi = {10.1149/2.0101707jes},
issn = {0013-4651, 1945-7111},
year = {2017},
date = {2017-01-01},
urldate = {2017-01-01},
journal = {Journal of The Electrochemical Society},
volume = {164},
number = {7},
pages = {A1339--A1341},
abstract = {3-dimensional (3D) electrode architectures have been explored as a means to decouple power and energy trade-offs in thick battery electrodes. Limited work has been published which systematically examines the impact of these architectures at the pouch cell level. This paper conducts an analysis on the potential capacity gains that can be realized with thick co-extruded electrodes in a pouch cell. Our findings show that despite lower active material composition for each cathode layer, the effective gain in thickness and active material loading enables pouch cell capacity gains greater than 10% with a Lithium Nickel Manganese Cobalt Oxide (NMC) materials system.},
keywords = {Co-extrusion},
pubstate = {published},
tppubtype = {article}
}
3-dimensional (3D) electrode architectures have been explored as a means to decouple power and energy trade-offs in thick battery electrodes. Limited work has been published which systematically examines the impact of these architectures at the pouch cell level. This paper conducts an analysis on the potential capacity gains that can be realized with thick co-extruded electrodes in a pouch cell. Our findings show that despite lower active material composition for each cathode layer, the effective gain in thickness and active material loading enables pouch cell capacity gains greater than 10% with a Lithium Nickel Manganese Cobalt Oxide (NMC) materials system. |
 | Cobb, Corie Lynn; Bae, Chang-Jun Three dimensional co-extruded battery electrodes Patent US9793537B2, 2017. @patent{cobb_three_2017,
title = {Three dimensional co-extruded battery electrodes},
author = {Corie Lynn Cobb and Chang-Jun Bae},
url = {https://patents.google.com/patent/US9793537/en},
year = {2017},
date = {2017-01-01},
urldate = {2018-03-05},
number = {US9793537B2},
abstract = {A three dimensional electrode structure having a first layer of interdigitated stripes of material oriented in a first direction, and a second layer of interdigitated stripes of material oriented in a second direction residing on the first layer of interdigitated stripes of material. A method of manufacturing a three dimensional electrode structure includes depositing a first layer of interdigitated stripes of an active material and an intermediate material on a substrate in a first direction, and depositing a second layer of interdigitated stripes of the active material and the intermediate material on the first layer in a second direction orthogonal to the first direction.},
keywords = {additive manufacturing, Co-extrusion, printed batteries},
pubstate = {published},
tppubtype = {patent}
}
A three dimensional electrode structure having a first layer of interdigitated stripes of material oriented in a first direction, and a second layer of interdigitated stripes of material oriented in a second direction residing on the first layer of interdigitated stripes of material. A method of manufacturing a three dimensional electrode structure includes depositing a first layer of interdigitated stripes of an active material and an intermediate material on a substrate in a first direction, and depositing a second layer of interdigitated stripes of the active material and the intermediate material on the first layer in a second direction orthogonal to the first direction. |
 | Cobb, Corie Lynn; Johnson, David Mathew Hierarchical laminates fabricated from micro-scale, digitally patterned films Patent US20170239929A1, 2017. @patent{cobb_hierarchical_2017,
title = {Hierarchical laminates fabricated from micro-scale, digitally patterned films},
author = {Corie Lynn Cobb and David Mathew Johnson},
url = {https://patents.google.com/patent/US20170239929A1/en},
year = {2017},
date = {2017-01-01},
urldate = {2018-03-13},
number = {US20170239929A1},
abstract = {A method of manufacturing a hierarchical laminate including forming a first hierarchical film, coating the first hierarchical film with an adhesive, stacking a second hierarchical film on the first hierarchical film, and curing the adhesive. A laminate structure has at least two electrohydrodynamic patterned film layers, the at least two layers being aligned and bonded.},
keywords = {architected materials, composite materials},
pubstate = {published},
tppubtype = {patent}
}
A method of manufacturing a hierarchical laminate including forming a first hierarchical film, coating the first hierarchical film with an adhesive, stacking a second hierarchical film on the first hierarchical film, and curing the adhesive. A laminate structure has at least two electrohydrodynamic patterned film layers, the at least two layers being aligned and bonded. |
 | Paschkewitz, John Steven; Cobb, Corie Lynn; Johnson, David Mathew; Iftime, Gabriel; Beck, Victor Alfred; Ng, Tse Nga; Rao, Ranjeet Method for roll-to-roll production of flexible, stretchy objects with integrated thermoelectric modules, electronics and heat dissipation Patent US9543495B2, 2017. @patent{paschkewitz_method_2017,
title = {Method for roll-to-roll production of flexible, stretchy objects with integrated thermoelectric modules, electronics and heat dissipation},
author = {John Steven Paschkewitz and Corie Lynn Cobb and David Mathew Johnson and Gabriel Iftime and Victor Alfred Beck and Tse Nga Ng and Ranjeet Rao},
url = {https://patents.google.com/patent/US9543495B2/en},
year = {2017},
date = {2017-01-01},
urldate = {2018-03-13},
number = {US9543495B2},
abstract = {A method of forming a flexible thermal regulation device having multiple functional layers. The layers of the device are formed using various manufacturing techniques and are then integrated to form a sheet having multiple devices disposed thereon. The individual devices are then formed from the sheet.},
keywords = {additive manufacturing, printed electronics, wearables},
pubstate = {published},
tppubtype = {patent}
}
A method of forming a flexible thermal regulation device having multiple functional layers. The layers of the device are formed using various manufacturing techniques and are then integrated to form a sheet having multiple devices disposed thereon. The individual devices are then formed from the sheet. |
2016
|
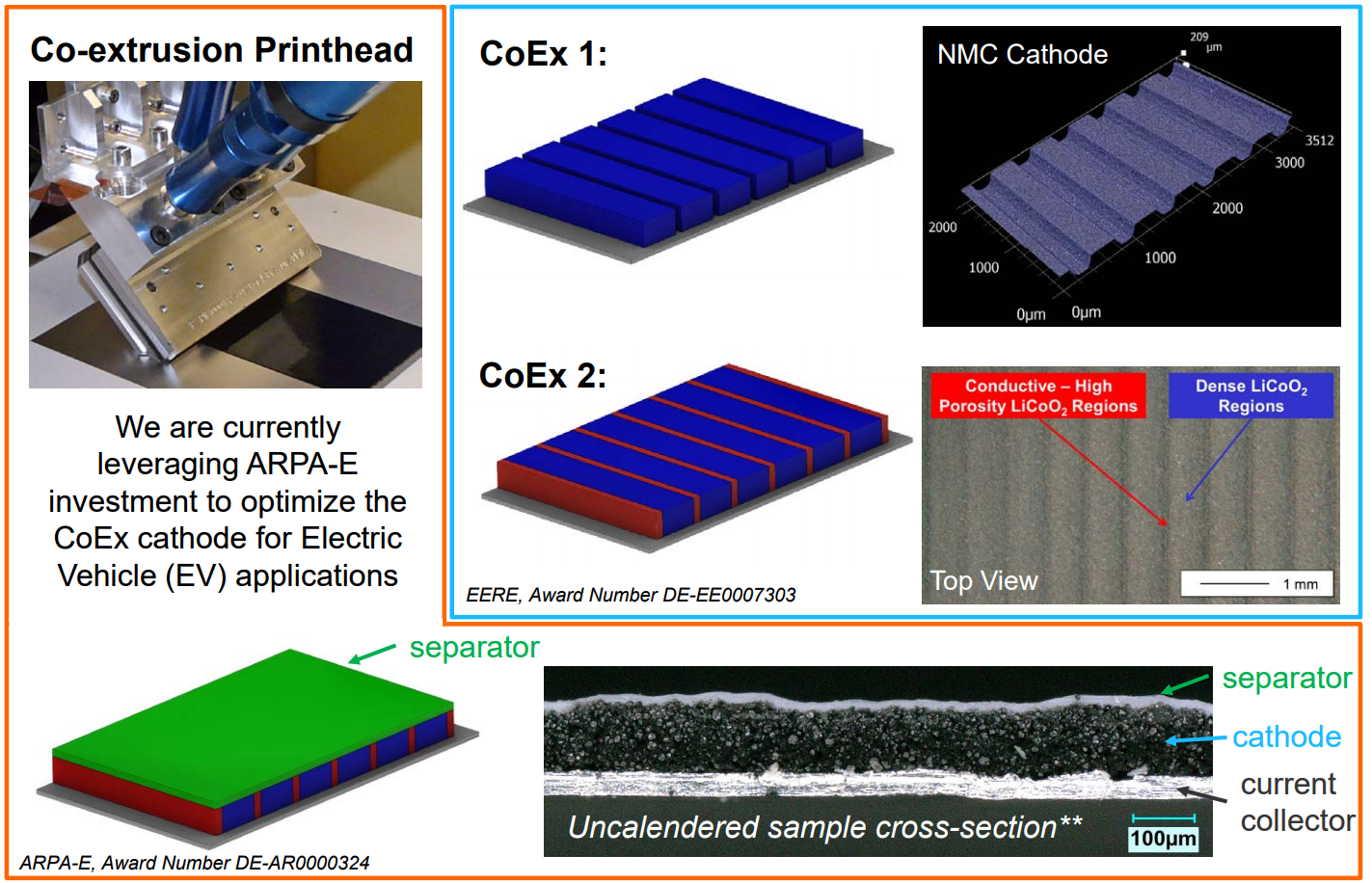 | Cobb, Corie Lynn Co-Extrusion: Advanced Manufacturing for Energy Devices Miscellaneous 2016. @misc{cobb_co-extrusion:_2016,
title = {Co-Extrusion: Advanced Manufacturing for Energy Devices},
author = {Corie Lynn Cobb},
url = {https://www.osti.gov/biblio/1333314},
year = {2016},
date = {2016-11-01},
urldate = {2018-03-14},
abstract = {The U.S. Department of Energy's Office of Scientific and Technical Information},
keywords = {additive manufacturing, Co-extrusion, printed batteries},
pubstate = {published},
tppubtype = {misc}
}
The U.S. Department of Energy's Office of Scientific and Technical Information |
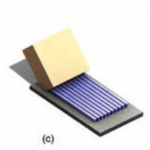 | Cobb, Corie L; Ho, Christine C Additive Manufacturing: Rethinking Battery Design Journal Article In: The Electrochemical Society Interface, vol. 25, no. 1, pp. 75-78, 2016, ISSN: 1064-8208, 1944-8783. @article{cobb_additive_2016,
title = {Additive Manufacturing: Rethinking Battery Design},
author = {Corie L Cobb and Christine C Ho},
url = {http://interface.ecsdl.org/content/25/1/75},
issn = {1064-8208, 1944-8783},
year = {2016},
date = {2016-01-01},
urldate = {2017-09-13},
journal = {The Electrochemical Society Interface},
volume = {25},
number = {1},
pages = {75-78},
abstract = {This article outlines emerging trends in the use of additive manufacturing techniques for the manufacture of batteries with customized geometries. Following a brief overview of conventional battery manufacturing, we discuss additive manufacturing strategies such as extrusion and dispenser printing, ink-jet printing, and screen printing in the context of battery manufacturing, and highlight the pros and cons of each technique. We provide some examples of 2D and 3D battery structures created by additive manufacturing, and highlight current and future research directions for battery design, manufacturing, and integration for small, portable and wearable electronics.},
keywords = {additive manufacturing, printed batteries},
pubstate = {published},
tppubtype = {article}
}
This article outlines emerging trends in the use of additive manufacturing techniques for the manufacture of batteries with customized geometries. Following a brief overview of conventional battery manufacturing, we discuss additive manufacturing strategies such as extrusion and dispenser printing, ink-jet printing, and screen printing in the context of battery manufacturing, and highlight the pros and cons of each technique. We provide some examples of 2D and 3D battery structures created by additive manufacturing, and highlight current and future research directions for battery design, manufacturing, and integration for small, portable and wearable electronics. |
 | Cobb, Corie Lynn Co-extrusion print head for multi-layer battery structures Patent US9337471 B2, 2016. @patent{cobb_co-extrusion_2016,
title = {Co-extrusion print head for multi-layer battery structures},
author = {Corie Lynn Cobb},
url = {http://www.google.com/patents/US9337471},
year = {2016},
date = {2016-01-01},
urldate = {2017-09-13},
number = {US9337471 B2},
abstract = {A co-extrusion print head capable of extruding at least two layers vertically in a single pass having a first inlet port connected to a first manifold, a first series of channels connected to the first inlet port arranged to receive a first fluid from the first inlet port, a second inlet port connected to one of either a second manifold or the first manifold, a second series of channels connected to the second inlet port arranged to receive a second fluid from the second inlet port, a merge portion of the print head connected to the first and second series of channels, the merge portion arranged to receive the first and second fluids, and an outlet port connected to the merge portion, the outlet port arranged to deposit the first and second fluids from the merge portion as a vertical stack on a substrate.},
keywords = {additive manufacturing, Co-extrusion, printed batteries},
pubstate = {published},
tppubtype = {patent}
}
A co-extrusion print head capable of extruding at least two layers vertically in a single pass having a first inlet port connected to a first manifold, a first series of channels connected to the first inlet port arranged to receive a first fluid from the first inlet port, a second inlet port connected to one of either a second manifold or the first manifold, a second series of channels connected to the second inlet port arranged to receive a second fluid from the second inlet port, a merge portion of the print head connected to the first and second series of channels, the merge portion arranged to receive the first and second fluids, and an outlet port connected to the merge portion, the outlet port arranged to deposit the first and second fluids from the merge portion as a vertical stack on a substrate. |
 | Cobb, Corie L; Hey, Jonathan; Agogino, Alice M; Beckman, Sara L; Kim, Sohyeong What Alumni Value from New Product Development Education: A Longitudinal Study Journal Article In: Advances in Engineering Education, vol. 5, no. 1, 2016. @article{cobb_what_2016,
title = {What Alumni Value from New Product Development Education: A Longitudinal Study},
author = {Corie L Cobb and Jonathan Hey and Alice M Agogino and Sara L Beckman and Sohyeong Kim},
url = {http://advances.asee.org/publication/what-alumni-value-from-new-product-development-education-a-longitudinal-study/},
year = {2016},
date = {2016-01-01},
urldate = {2018-03-05},
journal = {Advances in Engineering Education},
volume = {5},
number = {1},
abstract = {We present a longitudinal study of what graduates take away from a cross-disciplinary graduate-level New Product Development (NPD) course at UC Berkeley over a 15-year period from 1996-2010. We designed and deployed a longitudinal survey and interviewed a segment of our NPD alumni population to better understand how well our course prepared these alumni for careers in design, innovation, entrepreneurship and product management. We questioned alumni regarding the value of specific NPD skills, methods, and tools taught in the course. This paper presents a quantitative and qualitative analysis of survey and interview data. The results reaffirm the value of engaging students in multidisciplinary design projects as a means for developing the skills needed in today’s competitive NPD environment and highlight the similarities and differences that exist between academic and industry NPD practices. We believe the findings will inform educators about what is valued in NPD courses by graduates now working in industry.},
keywords = {engineering education, new product development},
pubstate = {published},
tppubtype = {article}
}
We present a longitudinal study of what graduates take away from a cross-disciplinary graduate-level New Product Development (NPD) course at UC Berkeley over a 15-year period from 1996-2010. We designed and deployed a longitudinal survey and interviewed a segment of our NPD alumni population to better understand how well our course prepared these alumni for careers in design, innovation, entrepreneurship and product management. We questioned alumni regarding the value of specific NPD skills, methods, and tools taught in the course. This paper presents a quantitative and qualitative analysis of survey and interview data. The results reaffirm the value of engaging students in multidisciplinary design projects as a means for developing the skills needed in today’s competitive NPD environment and highlight the similarities and differences that exist between academic and industry NPD practices. We believe the findings will inform educators about what is valued in NPD courses by graduates now working in industry. |
 | Johnson, David Mathew; Cobb, Corie Lynn Flexible thermal regulation device Patent US20160178251A1, 2016. @patent{johnson_flexible_2016,
title = {Flexible thermal regulation device},
author = {David Mathew Johnson and Corie Lynn Cobb},
url = {https://patents.google.com/patent/US20160178251/en},
year = {2016},
date = {2016-01-01},
urldate = {2018-03-14},
number = {US20160178251A1},
abstract = {A flexible temperature management device that uses powered thermoelectric elements to transfer thermal energy between a user and the environment to thermally regulate the user.},
keywords = {printed electronics, wearables},
pubstate = {published},
tppubtype = {patent}
}
A flexible temperature management device that uses powered thermoelectric elements to transfer thermal energy between a user and the environment to thermally regulate the user. |
2015
|
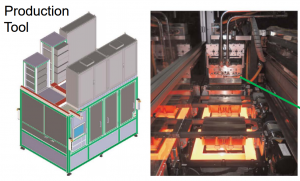 | Richter, Philipp L; Fischer, Gerd; Sylla, Lamine; Hentsche, Melanie; Steckemetz, Stefan; Müller, Matthias; Cobb, Corie L; Solberg, Scott E; Rao, Ranjeet; Elrod, Scott; Palinginis, Phedon; Schneiderlöchner, Eric; Neuhaus, Holger D Progress in fine-line metallization by co-extrusion printing on cast monosilicon PERC solar cells Journal Article In: Solar Energy Materials and Solar Cells, vol. 142, pp. 18–23, 2015, ISSN: 0927-0248. @article{richter_progress_2015,
title = {Progress in fine-line metallization by co-extrusion printing on cast monosilicon PERC solar cells},
author = {Philipp L Richter and Gerd Fischer and Lamine Sylla and Melanie Hentsche and Stefan Steckemetz and Matthias Müller and Corie L Cobb and Scott E Solberg and Ranjeet Rao and Scott Elrod and Phedon Palinginis and Eric Schneiderlöchner and Holger D Neuhaus},
url = {http://www.sciencedirect.com/science/article/pii/S0927024815002287},
doi = {10.1016/j.solmat.2015.05.023},
issn = {0927-0248},
year = {2015},
date = {2015-11-01},
urldate = {2018-03-05},
journal = {Solar Energy Materials and Solar Cells},
volume = {142},
pages = {18--23},
series = {Proceedings of the 5th International Conference on Crystalline Silicon Photovoltaics (SiliconPV 2015)},
abstract = {In this paper, we present our progress in co-extrusion printing for fine-line metallization. With this technique, 30µm wide and 20µm tall front grid fingers are currently printed. Applied to industrial size cast silicon PERC solar cells, a world record conversion efficiency of 21.42% has been demonstrated. This result was achieved with a production-ready co-extrusion printer that runs at a throughput of 2700 wafers per hour. Furthermore, a printhead is presented that has been developed to enable co-extrusion printing on pseudo-square wafers. Finally the cost advantage of the technology is discussed.},
keywords = {Co-extrusion, solar},
pubstate = {published},
tppubtype = {article}
}
In this paper, we present our progress in co-extrusion printing for fine-line metallization. With this technique, 30µm wide and 20µm tall front grid fingers are currently printed. Applied to industrial size cast silicon PERC solar cells, a world record conversion efficiency of 21.42% has been demonstrated. This result was achieved with a production-ready co-extrusion printer that runs at a throughput of 2700 wafers per hour. Furthermore, a printhead is presented that has been developed to enable co-extrusion printing on pseudo-square wafers. Finally the cost advantage of the technology is discussed. |
2014
|
 | Cobb, Corie Lynn Co-extrusion print head for multi-layer battery structures Patent US20140186519A1, 2014. @patent{cobb_co-extrusion_2014,
title = {Co-extrusion print head for multi-layer battery structures},
author = {Corie Lynn Cobb},
url = {https://patents.google.com/patent/US20140186519A1/en},
year = {2014},
date = {2014-07-01},
urldate = {2018-03-14},
number = {US20140186519A1},
abstract = {A co-extrusion print head capable of extruding at least two layers vertically in a single pass having a first inlet port connected to a first manifold, a first series of channels connected to the first inlet port arranged to receive a first fluid from the first inlet port, a second inlet port connected to one of either a second manifold or the first manifold, a second series of channels connected to the second inlet port arranged to receive a second fluid from the second inlet port, a merge portion of the print head connected to the first and second series of channels, the merge portion arranged to receive the first and second fluids, and an outlet port connected to the merge portion, the outlet port arranged to deposit the first and second fluids from the merge portion as a vertical stack on a substrate.},
keywords = {additive manufacturing, Co-extrusion, printed batteries},
pubstate = {published},
tppubtype = {patent}
}
A co-extrusion print head capable of extruding at least two layers vertically in a single pass having a first inlet port connected to a first manifold, a first series of channels connected to the first inlet port arranged to receive a first fluid from the first inlet port, a second inlet port connected to one of either a second manifold or the first manifold, a second series of channels connected to the second inlet port arranged to receive a second fluid from the second inlet port, a merge portion of the print head connected to the first and second series of channels, the merge portion arranged to receive the first and second fluids, and an outlet port connected to the merge portion, the outlet port arranged to deposit the first and second fluids from the merge portion as a vertical stack on a substrate. |
 | Cobb, Corie L; Blanco, Mario Modeling mass and density distribution effects on the performance of co-extruded electrodes for high energy density lithium-ion batteries Journal Article In: Journal of Power Sources, vol. 249, pp. 357–366, 2014, ISSN: 0378-7753. @article{cobb_modeling_2014,
title = {Modeling mass and density distribution effects on the performance of co-extruded electrodes for high energy density lithium-ion batteries},
author = {Corie L Cobb and Mario Blanco},
url = {http://www.sciencedirect.com/science/article/pii/S0378775313017503},
doi = {10.1016/j.jpowsour.2013.10.084},
issn = {0378-7753},
year = {2014},
date = {2014-01-01},
urldate = {2017-09-13},
journal = {Journal of Power Sources},
volume = {249},
pages = {357--366},
abstract = {Utilizing an existing macro-homogeneous porous electrode model developed by John Newman, this paper aims to explore the potential energy density gains which can be realized in lithium-ion battery electrodes fabricated with co-extrusion printing technology. This paper conducts an analysis on two-dimensional electrode cross-sections and presents the electrochemical performance results, including calculated volumetric energy capacity for a general class of lithium cobalt oxide (LiCoO2) co-extruded cathodes, in the presence of a lithium metal anode, polymer separator and liquid ethylene carbonate, propylene carbonate, and dimethyl carbonate (EC:PC:DMC) electrolyte. The impact of structured electrodes on cell performance is investigated by varying the physical distribution of a fixed amount of cathode mass over a space of dimensions which can be fabricated by co-extrusion. By systematically varying the thickness and aspect ratio of the electrode structures, we present an optimal subset of geometries and design rules for co-extruded geometries. Modeling results demonstrate that ultra-thick LiCoO2 electrodes, on the order of 150–300 μm, can garner a substantial improvement in material utilization and in turn capacity through electrolyte channels and fine width electrode pillars which are 25–100 μm wide.},
keywords = {battery modeling, Co-extrusion, printed batteries},
pubstate = {published},
tppubtype = {article}
}
Utilizing an existing macro-homogeneous porous electrode model developed by John Newman, this paper aims to explore the potential energy density gains which can be realized in lithium-ion battery electrodes fabricated with co-extrusion printing technology. This paper conducts an analysis on two-dimensional electrode cross-sections and presents the electrochemical performance results, including calculated volumetric energy capacity for a general class of lithium cobalt oxide (LiCoO2) co-extruded cathodes, in the presence of a lithium metal anode, polymer separator and liquid ethylene carbonate, propylene carbonate, and dimethyl carbonate (EC:PC:DMC) electrolyte. The impact of structured electrodes on cell performance is investigated by varying the physical distribution of a fixed amount of cathode mass over a space of dimensions which can be fabricated by co-extrusion. By systematically varying the thickness and aspect ratio of the electrode structures, we present an optimal subset of geometries and design rules for co-extruded geometries. Modeling results demonstrate that ultra-thick LiCoO2 electrodes, on the order of 150–300 μm, can garner a substantial improvement in material utilization and in turn capacity through electrolyte channels and fine width electrode pillars which are 25–100 μm wide. |
 | Cobb, Corie Lynn; Solberg, Scott E Micro-extrusion printhead with offset orifices for generating gridlines on non-square substrates Patent US8875653 B2, 2014. @patent{cobb_micro-extrusion_2014,
title = {Micro-extrusion printhead with offset orifices for generating gridlines on non-square substrates},
author = {Corie Lynn Cobb and Scott E Solberg},
url = {http://www.google.com/patents/US8875653},
year = {2014},
date = {2014-01-01},
urldate = {2017-09-13},
number = {US8875653 B2},
abstract = {A solar cell extrusion printing system that uses a micro-extrusion printhead to print longer central gridlines and one or more pairs of shorter “side” gridlines such that end points of the gridline sets form step patterns on an octagonal (pseudo-square) substrate. The printhead includes a set of central nozzles that receive ink from a first valve by way of a first flow channel to print the longer central gridlines, and additional sets of side nozzles that receive ink from additional valves by way of additional flow channels to print the shorter “side” gridlines. The central nozzles have outlet orifices that offset in the process direction from side outlet orifices of the side nozzles. A start signal is simultaneously sent to the valves such that ink is substantially simultaneously extruded through both the central and side orifices, whereby the extruded ink produces gridline endpoints having the desired step pattern.},
keywords = {Co-extrusion, solar},
pubstate = {published},
tppubtype = {patent}
}
A solar cell extrusion printing system that uses a micro-extrusion printhead to print longer central gridlines and one or more pairs of shorter “side” gridlines such that end points of the gridline sets form step patterns on an octagonal (pseudo-square) substrate. The printhead includes a set of central nozzles that receive ink from a first valve by way of a first flow channel to print the longer central gridlines, and additional sets of side nozzles that receive ink from additional valves by way of additional flow channels to print the shorter “side” gridlines. The central nozzles have outlet orifices that offset in the process direction from side outlet orifices of the side nozzles. A start signal is simultaneously sent to the valves such that ink is substantially simultaneously extruded through both the central and side orifices, whereby the extruded ink produces gridline endpoints having the desired step pattern. |
 | Cobb, Corie Lynn; Bae, Chang-Jun Tortuosity of Binder-Free and Carbon-Free High Energy Density LiCoO2 Electrodes for Rechargeable Lithium-Ion Batteries Proceedings Article In: ECS Transactions, pp. 13–24, The Electrochemical Society, 2014. @inproceedings{cobb_tortuosity_2014,
title = {Tortuosity of Binder-Free and Carbon-Free High Energy Density LiCoO2 Electrodes for Rechargeable Lithium-Ion Batteries},
author = {Corie Lynn Cobb and Chang-Jun Bae},
url = {https://iopscience.iop.org/article/10.1149/05813.0013ecst},
doi = {10.1149/05813.0013ecst},
year = {2014},
date = {2014-01-01},
urldate = {2018-03-05},
booktitle = {ECS Transactions},
volume = {58},
pages = {13--24},
publisher = {The Electrochemical Society},
abstract = {Conventional electrodes, by volume, contain a large amount of electrochemically inactive material such as binder and carbon. This lowers the overall capacity of a battery and makes it difficult to realize high volumetric energy. Researchers have been actively pursuing methods which will enable the fabrication and full utilization of thick electrodes (≥200µm) with a minimal amount of inactive material. One approach which has emerged is to fabricate thick sintered electrode structures which are free of binder and carbon. However, these structures do not adhere to conventional assumptions about tortuosity. This paper aims to correlate John Newman’s macrohomogeneous porous electrode model to thick high energy density, carbon-free and binder-free sintered electrode samples fabricated at PARC. We examine how assumptions about tortuosity affect model predictions of capacity. Our efforts focus on understanding the model parameters which can be used in Newman’s existing model without modification to the underlying equations.},
keywords = {battery modeling},
pubstate = {published},
tppubtype = {inproceedings}
}
Conventional electrodes, by volume, contain a large amount of electrochemically inactive material such as binder and carbon. This lowers the overall capacity of a battery and makes it difficult to realize high volumetric energy. Researchers have been actively pursuing methods which will enable the fabrication and full utilization of thick electrodes (≥200µm) with a minimal amount of inactive material. One approach which has emerged is to fabricate thick sintered electrode structures which are free of binder and carbon. However, these structures do not adhere to conventional assumptions about tortuosity. This paper aims to correlate John Newman’s macrohomogeneous porous electrode model to thick high energy density, carbon-free and binder-free sintered electrode samples fabricated at PARC. We examine how assumptions about tortuosity affect model predictions of capacity. Our efforts focus on understanding the model parameters which can be used in Newman’s existing model without modification to the underlying equations. |
 | Bae, Chang-Jun; Shrader, Eric J; Cobb, Corie Lynn Advanced, high power and energy battery electrode manufactured by co-extrusion printing Patent US20140186700A1, 2014. @patent{bae_advanced_2014,
title = {Advanced, high power and energy battery electrode manufactured by co-extrusion printing},
author = {Chang-Jun Bae and Eric J Shrader and Corie Lynn Cobb},
url = {https://patents.google.com/patent/US20140186700A1/en?inventor=Corie+Lynn+Cobb},
year = {2014},
date = {2014-01-01},
urldate = {2018-03-05},
number = {US20140186700A1},
abstract = {A battery has an anode, a separator adjacent the anode, and a cathode adjacent the separator opposite the anode, the cathode comprising interdigitated stripes of materials, one of the materials forming a pore channel.},
keywords = {additive manufacturing, Co-extrusion, printed batteries},
pubstate = {published},
tppubtype = {patent}
}
A battery has an anode, a separator adjacent the anode, and a cathode adjacent the separator opposite the anode, the cathode comprising interdigitated stripes of materials, one of the materials forming a pore channel. |
 | Cruse, James P; Lane, John W; Gregor, Mariusch; Buckius, Duc; Daran, Berrin; Cobb, Corie Lynn; Xu, Ming; Nguyen, Andrew Methods and apparatus for calibrating flow controllers in substrate processing systems Patent US8707754B2, 2014. @patent{cruse_methods_2014,
title = {Methods and apparatus for calibrating flow controllers in substrate processing systems},
author = {James P Cruse and John W Lane and Mariusch Gregor and Duc Buckius and Berrin Daran and Corie Lynn Cobb and Ming Xu and Andrew Nguyen},
url = {https://patents.google.com/patent/US8707754B2/en},
year = {2014},
date = {2014-01-01},
urldate = {2018-03-05},
number = {US8707754B2},
abstract = {Methods and apparatus for calibrating a plurality of gas flows in a substrate processing system are provided herein. In some embodiments, a substrate processing system may include a cluster tool comprising a first process chamber and a second process chamber coupled to a central vacuum transfer chamber; a first flow controller to provide a process gas to the first process chamber; a second flow controller to provide the process gas to the second process chamber; a mass flow verifier to verify a flow rate from each of the first and second flow controllers; a first conduit to selectively couple the first flow controller to the mass flow verifier; and a second conduit to selectively couple the second flow controller to the mass flow verifier.},
keywords = {semiconductor processing},
pubstate = {published},
tppubtype = {patent}
}
Methods and apparatus for calibrating a plurality of gas flows in a substrate processing system are provided herein. In some embodiments, a substrate processing system may include a cluster tool comprising a first process chamber and a second process chamber coupled to a central vacuum transfer chamber; a first flow controller to provide a process gas to the first process chamber; a second flow controller to provide the process gas to the second process chamber; a mass flow verifier to verify a flow rate from each of the first and second flow controllers; a first conduit to selectively couple the first flow controller to the mass flow verifier; and a second conduit to selectively couple the second flow controller to the mass flow verifier. |
 | Cobb, Corie Lynn; Xu, Ming Apparatus for controlling gas distribution using orifice ratio conductance control Patent US8905074B2, 2014. @patent{cobb_apparatus_2014,
title = {Apparatus for controlling gas distribution using orifice ratio conductance control},
author = {Corie Lynn Cobb and Ming Xu},
url = {https://patents.google.com/patent/US8905074B2/en},
year = {2014},
date = {2014-01-01},
urldate = {2018-03-05},
number = {US8905074B2},
abstract = {Apparatus for controlling gas distribution are provided. In some embodiments, apparatus for controlling gas distribution may include a first flow path from an inlet to a first outlet; a plurality of first orifices disposed within the first flow path; a plurality of first valves that control gas flow through the plurality of first orifices to control a total gas flow at the first outlet; a second flow path from the inlet to a second outlet; a plurality of second orifices disposed along the second flow path; a plurality of second valves that control gas flow through respective ones of the plurality of second orifices to control a total gas flow at the second outlet; and a mounting block having the plurality of first valves and second valves coupled thereto, wherein at least a portion of the first flow path and the second flow path is disposed within the mounting block.},
keywords = {semiconductor processing},
pubstate = {published},
tppubtype = {patent}
}
Apparatus for controlling gas distribution are provided. In some embodiments, apparatus for controlling gas distribution may include a first flow path from an inlet to a first outlet; a plurality of first orifices disposed within the first flow path; a plurality of first valves that control gas flow through the plurality of first orifices to control a total gas flow at the first outlet; a second flow path from the inlet to a second outlet; a plurality of second orifices disposed along the second flow path; a plurality of second valves that control gas flow through respective ones of the plurality of second orifices to control a total gas flow at the second outlet; and a mounting block having the plurality of first valves and second valves coupled thereto, wherein at least a portion of the first flow path and the second flow path is disposed within the mounting block. |
2013
|
 | Cobb, Corie Lynn; Solberg, Scott E Method For Generating Gridlines On Non-Square Substrates Patent US20130206220A1, 2013. @patent{cobb_method_2013,
title = {Method For Generating Gridlines On Non-Square Substrates},
author = {Corie Lynn Cobb and Scott E Solberg},
url = {https://patents.google.com/patent/US20130206220A1/en},
year = {2013},
date = {2013-08-01},
urldate = {2018-03-13},
number = {US20130206220A1},
abstract = {A solar cell production method involves printing longer central gridlines and one or more pairs of shorter “side” gridlines such that end points of the two gridline sets form step patterns on octagonal (pseudo-square) substrates. A special printhead is used that includes a set of central nozzles which receive ink from a first valve by way of a first flow channel to print the longer central gridlines, and additional sets of side nozzles that receive ink from additional valves by way of additional flow channels to print the shorter “side” gridlines. The central nozzles have outlet orifices that offset in the process direction from side outlet orifices of the side nozzles. A start signal is simultaneously sent to the valves such that ink is substantially simultaneously extruded through both the central and side orifices, whereby the extruded ink produces gridline endpoints having the desired step pattern.},
keywords = {Co-extrusion, solar},
pubstate = {published},
tppubtype = {patent}
}
A solar cell production method involves printing longer central gridlines and one or more pairs of shorter “side” gridlines such that end points of the two gridline sets form step patterns on octagonal (pseudo-square) substrates. A special printhead is used that includes a set of central nozzles which receive ink from a first valve by way of a first flow channel to print the longer central gridlines, and additional sets of side nozzles that receive ink from additional valves by way of additional flow channels to print the shorter “side” gridlines. The central nozzles have outlet orifices that offset in the process direction from side outlet orifices of the side nozzles. A start signal is simultaneously sent to the valves such that ink is substantially simultaneously extruded through both the central and side orifices, whereby the extruded ink produces gridline endpoints having the desired step pattern. |
2012
|
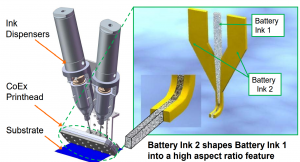 | Shrader, Eric J; Cobb, Corie L Co-Extrusion Printing for Low Cost and High Performance Energy Devices Proceedings Article In: Nanotechnology 2012: Bio Sensors, Instruments, Medical, Environment and Energy, pp. 537 – 540, NSTI, Santa Clara, CA, 2012, ISBN: 978-1-4665-6276-9. @inproceedings{shrader_co-extrusion_2012,
title = {Co-Extrusion Printing for Low Cost and High Performance Energy Devices},
author = {Eric J Shrader and Corie L Cobb},
url = {http://www.nsti.org/procs/Nanotech2012v3/8/T8.174},
isbn = {978-1-4665-6276-9},
year = {2012},
date = {2012-01-01},
urldate = {2018-03-05},
booktitle = {Nanotechnology 2012: Bio Sensors, Instruments, Medical, Environment and Energy},
volume = {3},
pages = {537 -- 540},
publisher = {NSTI},
address = {Santa Clara, CA},
abstract = {The method of co-extrusion of dissimilar materials has been developed at the PARC, a Xerox Company, to successfully produce high aspect ratio structures for solar cell gridlines. In the solar application, the process is stable and repeatable, and a fully integrated tool has been developed that is now being demonstrated at a customer site. The co-extrusion process is capable of non-contact, direct deposition of features as small as 1 – 10 um with aspect ratios in the range of 1:1 to 30:1. Alternating fluids are co-extruded to form a fine vertically interdigitated lamina structure. The relative thickness, width, and length of the deposited features can be varied by altering the printhead geometry and printing process conditions.},
keywords = {additive manufacturing, Co-extrusion, printed batteries, solar},
pubstate = {published},
tppubtype = {inproceedings}
}
The method of co-extrusion of dissimilar materials has been developed at the PARC, a Xerox Company, to successfully produce high aspect ratio structures for solar cell gridlines. In the solar application, the process is stable and repeatable, and a fully integrated tool has been developed that is now being demonstrated at a customer site. The co-extrusion process is capable of non-contact, direct deposition of features as small as 1 – 10 um with aspect ratios in the range of 1:1 to 30:1. Alternating fluids are co-extruded to form a fine vertically interdigitated lamina structure. The relative thickness, width, and length of the deposited features can be varied by altering the printhead geometry and printing process conditions. |
2011
|
 | Xu, Ming; Nguyen, Andrew; Lee, Evans; Lee, Jared Ahmad; Cruse, James P; Cobb, Corie Lynn; Salinas, Martin Jeff; Sheyner, Anchel; Gold, Ezra Robert; Lane, John W Twin chamber processing system Patent US20110265951A1, 2011. @patent{xu_twin_2011,
title = {Twin chamber processing system},
author = {Ming Xu and Andrew Nguyen and Evans Lee and Jared Ahmad Lee and James P Cruse and Corie Lynn Cobb and Martin Jeff Salinas and Anchel Sheyner and Ezra Robert Gold and John W Lane},
url = {https://patents.google.com/patent/US20110265951A1/},
year = {2011},
date = {2011-11-01},
urldate = {2018-03-05},
number = {US20110265951A1},
abstract = {Methods and apparatus for twin chamber processing systems are disclosed, and, in some embodiments, may include a first process chamber and a second process chamber having independent processing volumes and a plurality of shared resources between the first and second process chambers. In some embodiments, the shared resources include at least one of a shared vacuum pump, a shared gas panel, or a shared heat transfer source.},
keywords = {semiconductor processing},
pubstate = {published},
tppubtype = {patent}
}
Methods and apparatus for twin chamber processing systems are disclosed, and, in some embodiments, may include a first process chamber and a second process chamber having independent processing volumes and a plurality of shared resources between the first and second process chambers. In some embodiments, the shared resources include at least one of a shared vacuum pump, a shared gas panel, or a shared heat transfer source. |